1. What are the precautions for melting and casting fused cast AZS blocks to heat up?
2. What is the reason for the deterioration of physical and chemical indexes of fused cast AZS blocks?
3. How to judge the melting rate of glass furnace?
4. How to choose fused Cast AZS blocks for various parts of glass furnace?
5. How to achieve efficient thermal insulation of fused-cast AZS blocks?
6. How to determine the cooling air volume and cooling nozzle outlet speed of each part of the glass furnace?
7. How to test the effect of air-cooled side wall?
8. Selection requirements of arch blocks
9. Things to note when ordering fused cast AZS blocks
1. What are the precautions for melting and casting fused cast AZS blocks to heat up?
⑴ When the fused cast AZS blocks ignition temperature baking glass furnace, fused cast AZS block contains unstable plagioclase zirconia crystalline phase in the heating process will occur in the monoclinic - tetragonal phase transition, resulting in volume contraction; in the 1200 ~ 1550 ℃ critical temperature zone, with the increase in temperature in the glass furnace, fused cast AZS block of the glass phase began to exude. The higher the degree of oxidation, the more the remaining carbon is oxidized. The higher the degree of oxidation, the less remaining carbon (C ≤ 0.008%), Fe ₂ O ₃, TiO ₂, Ca0, Mg0 and other impurities, the lower the content (allowable content ≤ 0.4%), the higher the temperature of the glass phase exudation, the glass phase exudation is less.
That is to say, fused cast AZS blocks have small changes in physicochemical indexes and crystalline phases during ignition and glass furnace baking. The magnitude of the variation also varies with the difference in quality of the fused-cast AZS blocks.
⑵ Fused cast AZS blocks heating up at about 1150 ℃, cooling down near 850 ℃, there will be oblique zircon monoclinic and tetragonal irreversible phase transition brought about by the volume effect, resulting in abnormal contraction, expansion. If the temperature of the phase transition is not properly controlled during glass furnace baking, it is easy to produce blowout, transverse and longitudinal cracks (mostly longitudinal cracks).
A In the vicinity of the phase change temperature, the baking furnace temperature (the temperature of the crown thermocouple) heating should be slow and steady, and can not produce fluctuations. Therefore, in the heating curve of the baking glass furnace, it is required that the temperature of the crown in the 1250 ~ 1350 ℃ (crown temperature than the actual temperature of the sidewall is generally higher than 100 ~ 150 ℃), its heating speed should be controlled at 2.8 ℃ / h.
B Doghouse should be started at 1350 ℃ with special equipment to blow the broken glass (≤ 20mm) into the glass furnace, do not use the machine or manual charging, so that the cold broken glass piled up in the vicinity of the doghouse. Otherwise, the temperature fluctuation will be too large, caused by the volume effect of irreversible phase change of fused cast AZS blocks monoclinic and tetragonal, resulting in blow-ups and cracks.
C The over-fire temperature must be high and must not be lower than 1000℃. If the over-fire temperature is too low, it will lead to unstable combustion, causing the temperature inside the glass furnace to rise or fall sharply, resulting in a volume effect and causing the fused cast AZS blocks to burst; so if conditions permit, it is best to over-fire at 1200℃.
D The height of fused cast AZS blocks should preferably not exceed 2m, and do not choose fused cast AZS blocks that are too high and too large in size. Otherwise, it will lead to fused cast AZS blocks in the glass furnace baking process, in the 1/3 ~ 1/2 part of the blowing cracks, drop corner.
⑶ The Tuck stone fallout is mainly due to unreasonable design of the glass furnace structure or hooked block type. Reasonable glass furnace structure in the design should fully consider the center of gravity of the breast wall and support plate strength. Under the premise of the center of gravity of the breast wall and the strength of the support plate, the crown, the breast wall and the sidewall are separated and independently supported and reinforced. Leave an expansion joint of about 20mm between the crown and the breast wall, Leave 25~35mm expansion joints between the breast wall and the sidewall; Tuck stone fallout should also be designed to avoid stress concentrations, so that during glass furnace baking the tuck stone blocks do not fallout due to expansion and other factors.
⑷ When the Electrode Glass Furnace is baking, the electrode hole of the Feeder channel is broken down and the fused cast AZS blocks are melted, resulting in increased deformation of the electrode hole. The main reason is that the layout design of the electrode is not reasonable, resulting in lateral current, that is, current is generated between adjacent electrode holes on the same side.
2. What is the reason for the deterioration of physical and chemical indexes of fused cast AZS blocks?
⑴ Fused cast AZS blocks are used in glass furnace, after furnace baking and long-term contact with glass liquid, so glass phase exudation, glass liquid erosion, corundum dissolution, oblique zirconia and corundum eutectic aggregates become loose and so on, so that its physicochemical indexes and crystalline phase changes greatly. In addition, fused cast AZS blocks have segregation during casting.
The working surface part has high ZrO₂ content (up to 39% for PT fused cast AZS33# block), low volume density and low porosity, and strong resistance to vitreous liquid erosion.
Non-working surface part of ZrO₂ content is low (PT fused cast AZS33# block can reach 27%), porosity, weak resistance to glass liquid erosion.
The physical and chemical performance index specified in the specification refers to the measured value of the specimen cut from the 10mm thick and 15mm thick layers below the working surface after the work surface is removed by 20mm. After a period of operation, these parts have been eroded away, the remaining parts of its physical and chemical indicators and performance is certainly much worse than the original block.
⑵ The glass furnace was stopped due to an accident during operation. If not handled properly, the fused cast AZS blocks will explode and crack due to the volume effect caused by the irreversible phase transition of monoclinic and tetragonal zircon; if the fused cast AZS blocks are too large and the height exceeds 2m, the explosion and crack phenomenon will be more serious.
⑶ When a glass furnace has an accident, after the treatment is completed and the glass furnace is restarted, the number of years that it can be used again depends on the fused-cast AZS blocks. If the fused-cast AZS blocks are severely cracked and crazed, it will affect the service life of the glass furnace; in addition, it is also closely related to whether the remedial measures (such as increasing the cooling intensity) are effective.
3. How to judge the melting rate of glass furnace?
Melting temperature and regenerator temperature are related to glass formula, glass color, amount of cullet added, batch quality (raw material particle size, water content, mixing level) and requirements for melting quality. The design generally only limits the maximum melting temperature (large thermocouple temperature) (for example, if the melting rate reaches 3 tons/m², then T≤1600℃; if the melting rate is 2-2.5 tons/m², then T≤1570℃).
The switching time is generally 20 to 30 minutes. End fired glass furnace fueled by heavy oil and natural gas usually take 20 minutes. The switching time of End fired glass furnaces fueled by generator gas is slightly longer, generally 25 to 30 minutes. In short, each glass factory determines the switching time based on its own habits and equipment level.
The automatic control system of the necessary equipment should be determined according to the provisions of the "Access Conditions for Daily Glass": "Optimize and set up the computer control system to control the parameters of the glass furnace: temperature, furnace pressure, reversing, liquid level and air-fuel ratio, etc.; ensure the stability and accuracy of various process parameters during the glass melting process, so that the melting temperature control accuracy reaches ±3℃, low air-fuel ratio combustion is achieved, and the 0₂ content of the exhaust gas at the bottom of the regenerator is ≤1.6%."
According to the "Access Conditions for Daily-Use Glass" and "Basic Regulations for the Design of Daily-Use Glass Furnaces", it is not recommended to use the melting rate to evaluate glass furnaces. Instead, according to international practice, the glass furnace cycle melting rate is used to evaluate glass furnaces. The indicators are as follows:
indicator Product classification |
Glass Furnace cycle melting rate (t glass liquid/m ²) |
|
Glass beer bottle |
①≥5000 ②≥4000 |
|
glass bottle |
① |
③≥5000 |
④≥4200 |
||
② |
③≥4000 |
|
④≥3400 |
||
Note: ① refers to a glass furnace that uses heavy oil, natural gas, etc. as the main fuel; ② refers to a glass furnace using generator gas as the main fuel; ③ refers to ordinary glass frit (Fe2O3 ≥ 0.06%); ④ refers to high white materials (Fe2O3 < 0.06%). |
4. How to choose fused Cast AZS blocks for various parts of glass furnace?
The requirements for the side wall, throat, barrier wall, doghouse, working end paving and other parts should comply with the relevant provisions of the "Basic Regulations for the Design of Daily Glass Furnaces":
(1) When the sidewall is made of fused-cast AZS blocks, its height should not exceed 2m. If the size is too high or too large, the fused-cast AZS blocks will be severely segregated during casting, and they are prone to cracking and falling off during the glass furnace baking process.
(2) Article 5.1.4: "The sidewall should be built with large, vertically arranged, fused cast AZS blocks with basically no shrinkage cavities. When a double-layer sidewall is used, the upper layer is prohibited from using tilt cast fused cast AZS blocks. Void-free cast fused cast AZS blocks should be used. The joints between the upper and lower sidewall blocks after grinding should be ≤0.3mm to reduce the upward drilling erosion of the upper sidewall blocks by the glass liquid." The block joints of the sidewall masonry should comply with the requirements of the glass furnace installation, masonry and acceptance standards of China Light Industry International Engineering Co., Ltd. (BCEL): The block joints of the sidewall after masonry are 1 mm (the block joints after grinding are less than 0.5 mm, and then placed to 1 mm).
(3) Article 5.1.8: "The Barrier wall must be built with high-quality ZrO241% grade void-free fused-cast AZS blocks. The joints should be precisely ground, and the block structure designs must take into account the close fit during the glass furnace baking process." The block joints after grinding should be < 0.5 mm.
(4) Article 5.1.9: "The throat should be built with high-quality ZrO241% grade void-free cast fused-cast AZS blocks. The throat cover block can be built with void-free fused-cast AZS blocks (ZrO241% grade) with cast molybdenum plates on the inner layer of the surface." The block joints after grinding should be <0.5 mm.
(5) Article 5.1.10: "The doghouse corner block should be built with a whole piece of high-quality ZrO₂41% grade void-free fused-cast AZS blocks; colored soda-lime glass and boron glass furnaces can be built with fused-cast AZS blocks."
(6) Article 5.1.6: "The working end paving block should adopt a multi-layer structure with a thickness of 900-1100mm. The top of the working end paving block should be paved with a 75-150mm thick fused cast AZS blocks without shrinkage cavity; a 50-80mm main material sealing layer with basically the same crystal phase as the paving blocks should be set under the paving layer."
(7) Article 5.3.6: "The port neck, arch block and the tongue arch of the port of the generator gas melting furnace should be built with oxidation-fused cast AZS blocks with high glass phase seepage temperature." The block joints should be less than 1.5 mm, and the block joints should be poured with bulk powder (maximum particles <0.4mm) with basically the same crystal phase as the arch blocks.
(8) Regular-cast and tilt-cast fused cast AZS blocks must have the cast side facing outward because the working (non-cast) side of the block has a much higher ZrO₂ content than the cast side, and is more dense and resistant to glass furnace flyer (for the upper space) or to vitreous liquor (for the side wall) erosion. Regular cast and tilted cast blocks used as side wall applications with the cast opening facing inwards will allow the liquid glass to easily seep into the opening and erode through upward drilled holes, resulting in rapid erosion of the fused cast AZS block and a significant reduction in the quality of the liquid glass (increased streaking and stone formation).
5. How to achieve efficient thermal insulation of fused-cast AZS blocks?
(1) According to the provisions of the "Basic Regulations for the Design of Daily Glass Furnaces", it is no longer recommended to use regular casting and tilted casting fused cast AZS blocks for the working end and side wall, so there is no so-called insulation problem. If some factories insist on using it, the pouring port position of the tilt cast fused cast AZS block must meet the requirements of the BCEL specification, and the sidewall blocks can be fully insulated, but the upper 200-300mm of the sidewall must not be insulated and must be forced to cool. Regular casting blocks must not be used to build the working side wall, otherwise the periodic melting rate will be far from meeting the requirements of national and industry specifications.
Fused cast AZS Blocks with basically no shrinkage cavities and no shrinkage cavities can be fully insulated, but the upper 200-300mm part of the sidewall must not be insulated and must be forced to cool. When the side wall is insulated abroad, a gap of about 50mm is left between adjacent blocks. In China, 30-50mm of the main AZS ramming material with basically the same crystal phase as the block is poured behind the side wall blocks, and then clay bricks and efficient insulation layers are laid, and no block joints are left between adjacent blocks. The thermal insulation level of the working end sidewall is considered to be 8 to 15 degrees of insulation (see Table 5-5 of Article 5.5.1 of the "Basic Regulations for the Design of Daily Glass Melting Furnaces").
(2) The glass furnace paving must be designed in accordance with Article 5.1.6 of the "Basic Requirements for the Design of Daily Glass Furnaces": "The top of the paving should be paved with 75-150mm thick non-shrinkage fused-cast AZS blocks; a 50-80mm main material sealing layer with a crystal phase basically the same as that of the paving bricks should be set under the paving layer."
Some glass furnace fused cast AZS paving block will be corroded through, mainly because there is no body sealing layer with basically the same crystal phase as the paving tiles under the paving tiles, causing the glass liquid to penetrate from the brick joints to the bottom of the paving tiles, causing upward drilling erosion and causing the paving tiles to be corroded. Some refractory manufacturers use zircon ramming mass or waste fused cast blocks powder to make ramming mass. Since these ramming masses do not contain 18-20% of the glass phase in the fused cast AZS block, the paving blocks and the sealing layer cannot be sintered into a whole, causing the glass liquid to penetrate into the bottom of the paving blocks and produce upward drilling erosion. In addition, appropriate expansion joints must be left between the paving blocks and the sidewall blocks to ensure that the paving blocks will not be arched due to expansion during glass furnace baking.
(3) The bottom of the working end is made of large clay bricks, and the bottom should not be insulated, or when insulation is required, a gap of 50 to 100 mm must be left between adjacent bricks to prevent the clay bricks from floating (the r of the clay brick is 2.0 to 2.2, which is less than the r of the glass liquid, which is 2.5).
6. How to determine the cooling air volume and cooling nozzle outlet speed of each part of the glass furnace?
The distance between the working end and the melting end depends on the length of the throat, which is related to the type of glass liquid, the amount of material discharged and the cooling intensity of the throat. The length of the throat is generally 1000-1600mm (see "Basic Requirements for the Design of Daily Glass Furnaces" Article 5.19.)
The cooling air volume and cooling nozzle outlet velocity of each cooling part of the glass furnace shall comply with the requirements of Article 8.0.3 of the "Basic Provisions for the Design of Daily Glass Furnaces".
Cooling part |
Air volume |
Outlet wind speed |
Sidewall |
≥2700m³/h ·m |
>35m/s |
Doghouse corner |
≥2700m³/h · pcs |
>35m/s |
Throat |
≥2700m³/h ·m |
>35m/s |
Bubble block |
≥2700m³/h · pcs |
>15m/s |
Note: 1. The data in the table refers to the index of colored glass, and the index of colorless glass should be considered as 1.1 to 1.3 times; 2. The measured length of the throat refers to the sum of the width of the throat opening and the width of the two side walls (2×0.3m). |
The operating space at the port of the oil-fired glass furnace should be appropriately widened during design because:
① It can improve the working conditions of the operators and help improve the quality of glass;
② It will help with the future expansion of the glass furnace.
When designing glass furnaces abroad, the spacing is as follows: the distance between the inner side of the melting end (rear wall) and the inner side of the regenerator wall (rear gable wall) is generally controlled at 3.6 to 4 meters; However, there are certain restrictions on the renovation of glass furnaces in China, sometimes 2.8m. If the thickness of the regenerator wall and the glass furnace breast wall is not included, the net distance is only 1.35m (2.8m-0.7m-0.75m). This is what leads to poor operating conditions at the port. If the distance between the nozzle block and the rear gable wall is only 0.6m, the workers‘ operating conditions are very poor, and the high-temperature flame in the glass furnace radiates too strongly to the regenerator (because it is too close), the wall of the regenerator is prone to premature damage.
7. How to test the effect of air-cooled side wall?
The effect of air-cooled side walls is not only related to air volume and wind speed, but also to the thermal insulation of the blocks. The thinner the blocks, the lower the thermal insulation, and the better the cooling effect of the wind on the glass liquid on the inside of the sidewall.
When the residual thickness of the fused cast AZS blocks is very small, the thermal insulation of the block will be very low. The cooling effect of the cooling air on the glass liquid is extremely significant, so the glass liquid in contact with the side wall drops very low, the viscosity of the glass liquid increases, and the erosion of the fused cast AZS block will be sharply reduced. Therefore, under certain conditions, the glass furnace can work normally.
However, in actual operation, it is difficult to make the cooling air distribution intensity uniform due to the arrangement of the air nozzles around the glass furnace, and some glass furnaces have poor cooling effects in some parts due to unreasonable arrangement of the cooling nozzles. Therefore, when the residual thickness of the fused-cast AZS block is very small, accidents may occur due to some sudden reasons (such as power outages and air stoppages) or inadequate management; Therefore, frequent inspections and observations are necessary in the later stages of the glass furnace. If "red marks" are found on the side wall at night, measures should be taken as soon as possible, such as local strong cooling or tiling. For example, a glass factory in Shanghai, China adopted fused-cast AZS blocks (75mm thick) to patch the side wall in 2005 and used it for another 4 years (the glass furnace age was more than 12 years).
8. Selection requirements of arch blocks
The design of the tongue arch of a glass furnace using producer gas as fuel should strictly comply with the requirements of Article 5.3.6 of the "Basic Regulations for the Design of Daily Glass Furnaces": "The tongue arch should be built with oxidation-cast AZS blocks with high glass phase seepage temperature. When the tongue arch is built with blocks of different materials, the arch foot should be made of independently reinforced and individually adjusted steel structure. Effective sealing measures should be taken at the top of the tongue arch to prevent the tongue arch from burning.
When the tongue arch is built with different materials such as fused cast AZS blocks and silica bricks, due to the large difference in expansion coefficients of the two during the glass furnace baking process, If the adjustment is made according to the expansion coefficient of the silica brick, the fused cast AZS block crown will fall off; if the adjustment is made according to the expansion coefficient
of the fused cast AZS block, the silica brick crown will bulge and crack, and even cause the tie rod to break. Therefore, zircon fine slurry should be used for transition where the two different materials of blocks, fused cast AZS block arch and silica brick arch, come into contact.
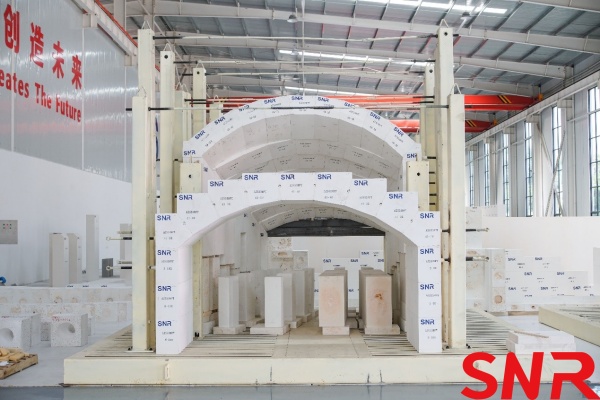
The crown should be built with
high-quality silica bricks or special-grade silica bricks, and should comply with the requirements of Section
s 5.1.13 to 14 of the "Basic Regulations for the Design of Daily Glass Furnaces".
The use of regenerator block should comply with the provisions of Section 5.4 regenerator in the "Basic Requirements for the Design of Daily Glass furnaces" and select the corresponding materials according to Table 6-1 in Section 6.0.1.
If the materials for each part of the glass furnace are strictly selected according to the provisions in Table 6-1 of Article 6.0.1, and the requirements for each part in the "Basic Regulations for the Design of Daily Glass Furnaces" are followed, and combined with scientific management, the cycle melting rate of the glass furnace can meet the requirements of the "Access Conditions for Daily Glass".
9. Things to n0te when ordering fused cast AZS blocks
(1) Quality acceptance criteria
The surface of fused cast AZS blocks should be flat and smooth, without obvious cracks, blisters, air holes and other defects, the edges and corners should be neat, and the color should be even, without obvious color difference.
The dimensions of fused cast AZS blocks should be in accordance with the design requirements, and the tolerances of length, width and thickness should be within the specified range.
Physical properties such as compressive strength, density, water absorption and abrasion resistance shall comply with national standards or contractual technical requirements.
(2) Other Notes
The contract for ordering fused-cast AZS blocks is a restriction on both parties. From the perspective of refractory material manufacturers, when users require high service life of glass furnaces and glass quality, the following requirements should be put forward:
The design of glass furnace should meet the basic requirements of "daily glass melting furnace design", the chemical composition of glass should meet the unified standard of "basic range of daily glass chemical composition", the quality of batch material should meet the general provisions of "batch material quality control", and the quality of glass furnace masonry should meet the relevant construction specifications and inspection and evaluation standards of glass melting furnace. Only by meeting all the above requirements can the glass furnace achieve the ideal life.
However, it should be pointed out that manufacturers of fused cast AZS blocks must strictly follow the requirements of JC493-2001 standard and Article 6.0.2 of "Basic Regulations for the Design of Daily Glass Fur
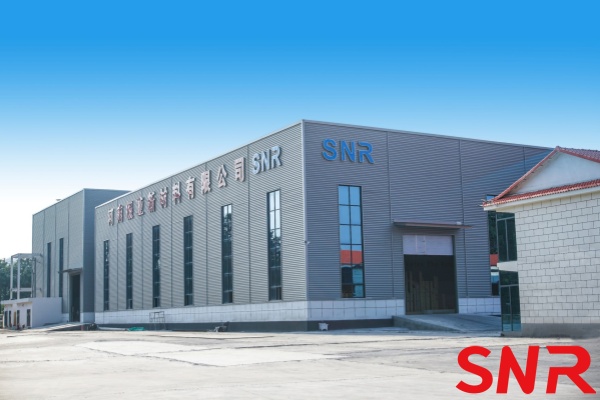
naces" to produce high-quality fused cast AZS blocks. Therefore, excessive price reduction in ordering cannot guarantee the quality of fused cast AZS blocks. It is necessary to explain from various aspects such as technical level that fused cast AZS blocks must maintain a moderate price. This requires the factory sales staff to have good knowledge of fused cast AZS blocks manufacturing.
Henan SNR Refractory Co., Ltd (SNR) is professional in producing high-quality Fused Cast AZS Blocks for glass furnaces. If you have any needs, please contact me!
zoe@snrefractory.com