The occurrence of zirconia stones is a “catastrophic” production accident for glass manufacturing factories. If it is not due to uncontrolled control of the glass melting process, it usually cannot be eliminated. Even if it is mitigated or alleviated, there are associated losses.
In this article, we discuss the identification characteristics of zirconia stones, the mechanism of their generation, and their prevention and control.
1. Identifying features of zirconia stones
1.1 Appearance Characteristics
Zirconium stones in glass mainly originate from zirconium refractory materials and zirconium clays in different parts of the glass furnace. Zirconium refractory materials and zirconium clay due to the different microstructure before entering the glass liquid, entering the glass liquid in different parts and temperatures, the formation of glass stones will also have a different appearance and microstructure. Most of the stones in the glass become white, grayish-white dense small granules, which are well-defined from the glass matrix and have a hard porcelain texture (Figure1). Plagioclase zircon can be
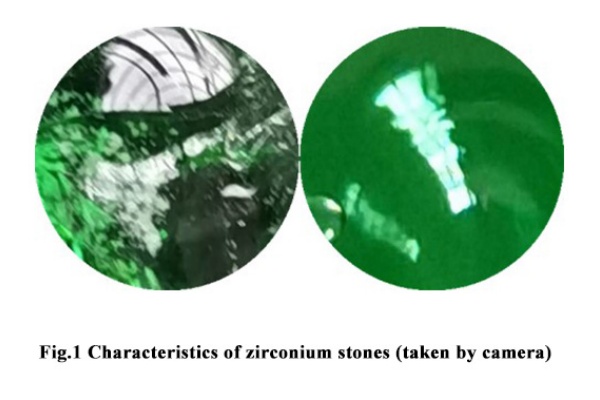
categorized into primary plagioclase, secondary plagioclase, and primary and secondary plagioclase zircon, and there is no major difference in the appearance of the three.
The structure of the stones formed by the zircon batter falling into the vitreous solution is usually loose; the outgrowth of the immobile layer at the furnace bottom is often well developed and intact, and most of them are quadratic plagioclase zircon, with typical crystalline phase structure characteristics.
1.2 Microscopic characteristics
Fused cast AZS block erosion from the melting end tends to form primary plagioclase zircon. Under the microscope, it is finely granular or spun humorous, ovoid distribution (Figure2 left); there are large internal pockmarks, the interface is uneven, and there are grain-mounted crystals in the boundary layer with the glass. Sometimes yellow-brown (Figure2 right), grain-mounted crystals; refractive index, high birefringence, extinction angle is not obvious.
Primary plagioclase zircon is dissolved at high temperatures and recrystallized in
glass
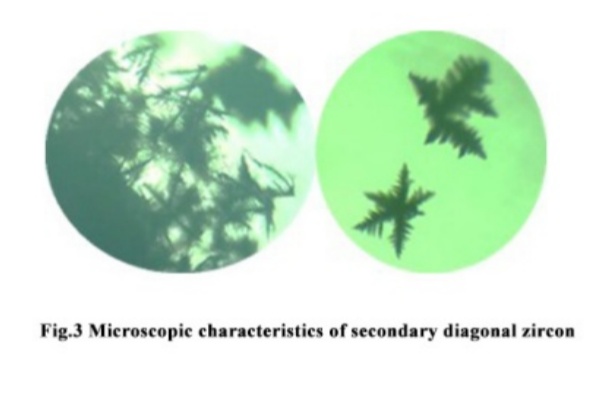
2. Erosion process of Fused cast AZS block
The erosion of fused cast AZS blocks is a process of dissolution of polycrystalline phase material, and the erosion process is divided into three steps:
2.1 Fused cast AZS block Melting
The melting of a fused cast AZS block consists of the precipitation of the glass phase into the glass solution (at which point holes are created in the fused cast AZS block), and the melting of plagioclase zircon and corundum fines by the glass solution to produce zircon and mullite:
Since the surface tension of the fused cast AZS block is lower than that of the glass solution, the glass solution is always infiltrated by the fused cast AZS blocks, and the size of the melt rate depends on the temperature and amount of the glass phase precipitated and the viscosity of the melt.
2.2 The molten layer leaves
The viscosity of the surface layer of the block in contact with the glass liquid increases, forming a high-viscosity protective layer on the block, thus preventing further erosion of the block by the glass liquid. When the glass furnace temperature increases or the liquid flow fluctuation is large, so that the original fused cast AZS block surface of the molten layer left the original position into the glass liquid. The speed of departure is related to the viscosity of the molten layer and the flow rate of the liquid glass. The erosion of fused cast AZS blocks at the doghouse corner, the liquid surface line of the side wall (Figure 4), and the throat of the flame furnace is usually much more serious than that of other parts.
2.3 Vitreous fluid penetration
When the molten layer on the surface of the fused cast AZS blocks leaves, new surfaces and pores are exposed, allowing the glass liquid to erode them for further melting. Penetration rate and diffusion rate and the structure of the fused cast AZS block, such as pore size, shape, number, distribution.
The above three processes are carried out over and over again, will make the fused cast AZS block erosion, especially the three-phase interface erosion. In practice, when zirconia stones appear, if the melting temperature is appropriately lowered, it is effective in reducing the erosion of the fused cast AZS block and improving the proportion of stones.
3. Causes of zirconia stones
3.1 Excessive introduction of fluxing components
3.1.1 Excessive anthropogenic introduction
In order to excessively pursue the melting rate, some glass factories have introduced a large number of high amounts of halogen components or other components that have a strong erosive effect on the fused cast AZS block, such as raw materials containing fluorine and chlorine, resulting in increased erosion of the glass furnace refractories materials.
3.1.2 Excessive introduction of fault
The so-called negligent introduction, i.e., the unintended introduction of higher amounts of fluxing components in unintended circumstances, usually occurs in the following cases:
•Errors in bin weighing, e.g. raw material with high content of ultrafine powder, automatically sliding into the weighing bin when weighing.
•Ignoring the fluorine content of some raw materials, leading to excessive introduction.
3.2 Melt temperature is proposed to be too high
Excessive melting temperatures are sometimes easily overlooked. In the pursuit of melting efficiency and the rate of pile disappearance, the rate of erosion of fused cast AZS block is also immediately obvious. In the case of high zirconia stones, controlling the melting temperature appropriately will make it easier to reduce the stone ratio rapidly.
3.3 Fused cast AZS block Selection Quality
There are two aspects covered here:
♦Fused cast AZS blocks material quality conditions, including chemical composition and physical properties of the indicators to achieve the situation;
♦Glass furnace design, according to different parts of the glass furnace refractory erosion resistance of different types of fused cast AZS blocks;
4. Preventive measures for zircon stones
4.1 Fused cast AZS block aspects
Selection of high quality fused cast AZS blocks. In JC/T 493 standard of fused cast AZS refractory products for glass melting furnace, it is required that the initial precipitation temperature of glass phase is ≥1400℃, and the amount of glass phase exudation (1500℃×4h) of AZS33-Y is less than or equal to 2.0%, and the amount of AZS36-Y and AZS41-Y is required to be less than 3.0%.
►Refractory material Hot Repair
For the eroded but repairable zirconium mullite, zirconium quartz and other related refractory materials should be hot repaired in a timely manner to prevent the erosion of the increased amount of stones brought about by the rise in the amount of stones.
►Selection of refractory materials
Different parts of the glass furnace on the refractory quality needs to be different, according to the special purpose of the corresponding refractory types, to avoid the material selection brought about by the erosion of the trouble.
For some easy to react at high temperatures of the refractory material, but also to avoid them directly masonry together.
4.2 Formulation Design Considerations
►Avoid secondary introduction of zirconia stones into the furnace
Outsourced crushed glass or “back material” that has developed zirconium stones must be removed before use. On the contrary, when entering the glass furnace for the second time, the large stones are still difficult to melt off completely, and the small stones will continue to precipitate or form streaks or nodules.
►Reducing dust emissions from compounding materials
The structure of the charging machine, the moisture content of the feed material, the control of the particle size of the feed material and other related measures can be used to reduce the contact of the feed material feeding fines into the glass furnace with the fused cast AZS block and aggravate the erosion of the material.
At the same time, it is necessary to strengthen the protection of the side wall blocks to avoid direct contact of the glass furnace materials with the sidewall blocks.
►Scientific use of fluxing auxiliary materials
Auxiliary raw materials for fluxing and clarifying, small dosage, big effect. Therefore, it needs to be used scientifically and carefully. To avoid excessive pursuit:
♦Extremely high melting rate;
♦Extremely thin foam side;
♦Zero pile runs.
Everything is result-oriented. The scientific selection of the type of auxiliary raw materials and their introduction in the right quantities is only of paramount importance when it comes to ensuring the requirements for glass furnace life, melt quality, melt energy consumption, product quality and molding system.
4.3 Melting process system
►Control the flame angle and length
Prevent fused cast AZS block erosion and zirconia-quartz tamping material from falling into the glass due to the flame.
►Preventing severe scouring of sidewall blocks
Stable melting temperature and discharge volume control system can reduce the fluctuation of glass liquid flow and prevent serious scouring of sidewall and upturning of glass liquid at the bottom of the melting end.
►Avoid excessive pursuit of high melting rate
The melting rate is suitable. Excessive pursuit of melting rate, increase the glass furnace temperature, will make the glass liquid and fused cast AZS blocks react violently; At the same time, the fluctuations in the amount of material discharged to the three-phase interfaces of the scouring will also be intensified.
4.4 Raw material control
►Strict screening of raw materials:
Fine screening of zirconium-containing raw materials such as zirconia is the first step in preventing zirconium stones. Purchase high-quality zircon and ask the supplier to provide a detailed composition analysis report of the raw materials to ensure that the content of impurities in them meets the production requirements. For example, metal oxides such as iron and titanium in the impurities, if the content is too high, may react with zircon during the high temperature process to form low melting point compounds, which in turn produce stones. Therefore, zircon with high purity should be used, and the general purity should be more than 95%.
Screen the incoming raw materials for particle size. If the zircon particles are too large, it will be difficult to disperse them evenly in the subsequent mixing and molding process, which will easily lead to local enrichment and the formation of stones. Usually, the particle size of zircon is controlled in a suitable range, such as through screening to make most of the particle size between 40 - 100 mesh, which will help its uniform distribution in the fused cast AZS blocks.
►Raw material pretreatment:
Pretreatment of zircon raw materials can effectively reduce the influence of impurities. For example, washing is used to remove dirt, dust and other impurities from the surface of the raw material. Because these impurities may contain some components that will react with zircon at high temperatures. After washing, drying can also be carried out to reduce the moisture content of the raw material to a suitable level, generally controlled at 0.5% or less, in order to avoid the subsequent high temperature process due to water evaporation to produce porosity and other defects, and indirectly prevent the formation of stones.
For some zircon containing more impurities, magnetic separation or flotation can be used to further purify. Magnetic separation can remove the magnetic impurities, such as iron filings, etc.; flotation can be based on the differences in the surface properties of zircon and other impurity minerals, to separate them and improve the purity of raw materials.
5. Summary
The root cause of zirconia stone is directly related to the quality of fused cast AZS blocks, glass furnace materials, glass formula design and adjustment, and the control of glass furnace melting system. The development of high erosion-resistant fused cast AZS blocks, improving the quality of fused cast AZS blocks, and the selection of targeted zirconium refractories according to the ease of erosion in different parts of the glass furnace are the prerequisites and bases for the improvement of zirconium nodules;
The scientific design of the formula components, the selection and adjustment of auxiliary raw materials and the stable melting process system are important guarantees to slow down the production of zirconia stones, especially in the early stage of the glass furnace life, which can basically eliminate the defects of zirconia stones. From the point of view of the erosion mechanism and process control, stable feed quantity, liquid level fluctuation, melting temperature, glass furnace pressure and flame adjustment are of great technological importance in slowing down the erosion of fused cast AZS blocks.
Henan SNR Refractory Co., Ltd. is dedicated to the manufacturing and research and development of fused cast AZS refractory materials for the glass industry. Meanwhile, SNR can provide total solutions and services for glass furnace design, glass furnace construction, renovation and upgrading. Please contact me if you have any requirement.