With the continuous improvement of refractory material quality and performance, it provides a basic condition for extending the service life of glass furnaces, making them more productive, energy-saving and reducing consumption, and producing high-quality glass products. Based on years of research, this article will discuss the selection of refractory materials for glass furnaces from the perspective of the dynamics of fused cast AZS blocks against glass liquid corrosion, and provide some scientific basis for the correct use of refractory materials in glass factories.
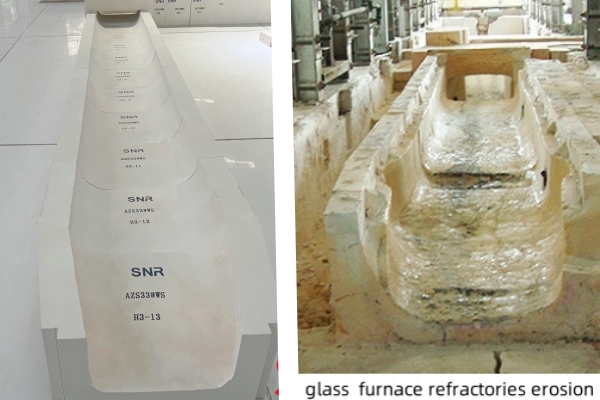
3. Effect of impurity content and valence state
6. Film formation reaction of fused cast AZS block
Fused cast AZS block is mainly composed of
• scattered baddeleyite
• corundum phase
• glass phase
SiO₂ and trace amounts of B₂O₃, FeO, Fe₂O₃, TiO, TiO₂, ZrO₂, Al₂O₂, CaO, MgO, K₂O, Na₂O, etc. form glass phases, which are filled between the crystal phases.
Therefore, the AZS products we produce require that the SiO₂ content be reduced as much as possible without cracking the product, so as to improve the corrosion resistance of the product. There are many factors that affect the cracking of the product, which will not be detailed here.
In the process of fused cast AZS production, some carbon will inevitably penetrate from the electrode, and some of it will eventually remain in the material.Carbon exists in the form of C, CO, and CO₂.
From the reaction formula 2C+O₂→2C0 and 2C0+0₂→2C02, it can be seen that the glass liquid contains many oxidizing components, which provide enough oxygen molecules for carbon.
From the above reaction, it can be seen that after 1 gram molecule of carbon is oxidized, 1 gram molecule of CO₂ gas will be formed, and 1 gram molecule of CO₂ is 22.4L under standard conditions. The temperature at the general glass liquid surface is 1500℃.
According to
V/Vo=T/To,
V=V₀(273+1500)/273=145L,
that is, 1 gram molecule of carbon will produce 145L.
C0₂ gas after oxidation, and this reaction is an exothermic reaction, which can further increase the temperature of the surrounding glass liquid. The gas volume expansion process is like a compression pump, which accelerates the seepage of the glass phase, prompting the rapid exchange of the glass phase components with the glass liquid components, further melting the crystal structure of the refractory material, and finally causing the rapid erosion of the material. This theory has been recognized by refractory material factories and glass factories.
Solution:
In order to reduce the carbon content in fused cast AZS blocks, our factory adopts oxidation electric melting process, through long arc melting and oxygen blowing to oxidize carbon as much as possible in liquid state, and the carbon content of the product is only 0.001% to 0.005%.
3. Effect of impurity content and valence state
Another major factor affecting AZS’s resistance to glass erosion is impurities, such as Fe²+, Fe³+, Ti⁴+, Ti²+, Ua²+ and Mg²+. They exist in the glass phase and form a low eutectic with SiO₂.
The more impurities there are, the lower the viscosity of the glass phase at high temperature and the lower the seepage temperature, which seriously affects the material’s ability to resist erosion. The main channel for bringing in impurities is raw materials.
During the production process, we strictly control the raw materials and strictly inspect the main raw materials entering the factory. It is required that the iron and titanium content in zircon sand is less than 0.25% and the content of Al₂O₃, the main component of alumina, is greater than 98.5%.
The valence state of impurities is also an important factor affecting the precipitation temperature of the glass phase of the product. The impurities of products produced by the reduction method are low-valent, while the impurities of products produced by the oxidation method are high-valent. The eutectic formed by low-valent impurities has a higher eutectic point than the low-valent impurities formed by valence impurities.
Table 1 lists the comprehensive results of different production processes and performance of 14 samples.
Table 1 Performance comparison of samples produced by different processes
Production process |
Oxidation method 33#AZS |
Reduction method 33#AZS |
Static resistance to glass liquid corrosion (mm/24h) |
1.30~1.41 |
1.41~1.86 |
Glass phase initial precipitation temperature (0) |
1400~1450 |
980~1080 |
Note: The test is to immerse the AZS sample in 1500% ordinary soda-lime glass and measure the single-side corrosion amount of the three-phase interface after 36 hours.
For glass factories, the main concerns are the color, bulk density and appearance of refractory materials, and the influence of microstructure on product performance is not taken seriously.
Generally speaking, AZ eutectoids are abundant and fully developed in fused cast AZS products, distributed in long strips or sheets, interweaving into a skeleton network, and the glass phase fills in between and is evenly distributed. If the baddeleyite in the glass phase is evenly distributed in the form of beads, the material has better resistance to glass liquid erosion. To this end, the Refractory Institute and the Pilot Plant of China Building Materials Research Institute have obtained preliminary results after several tests. Table 2 is the comparative data of a certain institute‘ products and SEFPRO‘ products.
Table 2 Comparison between a certain product and SEFPRO’s product (volume %)
Sample |
Corundum |
Eutectic |
Glass phase |
Porosity |
Glass erosion resistance(same conditions as in Table 1) (mm/24h |
94120019 (ER1681) |
10.0 |
61.5 |
21 |
2.8 |
|
94120020 (AZ833#) |
10.1 |
60.3 |
21 |
3.0 |
0.178 (CRT glass) |
94120021 (HR1711)* |
8.5 |
60.5 |
18 |
3.0 |
|
94120022 (AZS33#) |
9.5 |
60.0 |
18 |
3.2 |
1.0 |
Closed pores, i.e. dispersed pores, in fused cast AZS blocks are also important factors affecting its corrosion resistance.
On the one hand, the pores contain gas, and at 1500℃, the volume increases by 6.5 times, forming high pressure. As mentioned above, it will accelerate the glass phase seepage.
More importantly, the existence of pores increases the contact area with the glass liquid, which undoubtedly accelerates the erosion rate. A certain institute cooperated with the refractory institute to propose a series of process measures to produce high-density products.
After two years of use in the furnace of Shijiazhuang Baoshi Group, its erosion degree and bubble precipitation rate are very close to those of similar products of SEFPRO Company.
However, not all parts of fused cast AZS blocks require low pores. For example, the checkerboard bricks of the regenerator require high porosity. The cross-shaped chimney bricks jointly developed by the refractory institute and a certain institute were used by Yiyang Light Bulb Factory, and their thermal shock resistance and energy-saving effects are very good.
6. Film formation reaction of fused cast AZS block
As mentioned above, since the glass phase inevitably seeps out during the use of fused cast AZS blocks in the glass furnace, baddeleyite, corundum and its eutectoids are also wrapped in the glass phase.
In this process, baddeleyite and corundum are gradually dissolved in the glass phase, and a protective layer of high-refractory materials rich in ZrO₂ and Al₂O₃ is formed at the seepage site. Because they are affected by the lateral pressure (F₁) of the glass liquid and the buoyancy (F₂) of the thermal convection of the glass liquid, they will not quickly separate from the body (see Figure 1). However, if a large amount of glass phase seeps out and a large amount of bubbles in the refractory are discharged, it will leave the body and settle quickly.
In order to achieve good adhesion of the protective layer, the first thing is to keep the glass liquid surface stable.
♦ If the liquid level changes greatly, as the liquid level drops, F1 and F2 disappear at the same time, and the protective layer also drops.
♦ When the liquid level rises, the original protective layer has been separated from the main body, and a new protective layer must be created, thus accelerating the erosion rate.Maintaining a stable temperature field in the glass furnace is also an important factor.
♦ If the temperature field is unstable, the convection of the glass liquid will be unstable.
♦ If F₂ is not constant, it will inevitably make it difficult for the protective layer to achieve a good adhesion state and settle, which is also a key factor affecting refractory materials.
In the middle and late stages of block use, glass factories generally strengthen wind cooling on the outer side wall at the liquid surface to reduce local temperature, effectively reduce glass phase precipitation and stabilize the reaction interface layer structure, and delay erosion.
Uniformity and volume density of blanks during firing; at the sealing temperature, there is only a small volume shrinkage. To obtain a dense ceramic structure without micropores, it must be solved during pre-sintering.
7. Summary
As the key refractory material of glass furnace, the fused cast AZS block‘s resistance to glass liquid erosion is crucial to the service life of the furnace and the quality of glass.
The main factors affecting the erosion resistance of AZS blocks include
• SiO₂ content,
• carbon content,
• impurities and their valence,
• microstructure,
• closed pores
• film-forming reaction during use.
⇒Optimizing SiO₂ content, reducing carbon content, strictly controlling impurity content and valence, improving microstructure and reducing closed pores can all improve the erosion resistance of AZS blocks.
In addition, maintaining the stability of the glass liquid level and the temperature field of the glass furnace, as well as adopting appropriate cooling measures, can also help delay the erosion of AZS blocks. Therefore, when selecting and using AZS blocks, glass factories should comprehensively consider the above factors to ensure high production of glass furnaces, energy saving and consumption reduction, and the production of high-quality glass products.
♦ At the same time, refractory manufacturers should also continuously optimize production processes and improve product quality to meet the needs of the glass industry.
Henan SNR Refractory Co., Ltd. has been specializing in the production of fused cast AZS blocks for about 25 years. We use high-quality raw materials and advanced fusion technology to provide customers with high-quality products. From raw material procurement to finished product delivery, every step is strictly quality inspected to ensure that every indicator meets the standards, so you can use it with confidence.
If you have any needs, you can contact me at any time.
Web:www.snr-azs.com
Email:wendy@snrefractory.com