The design, material selection, construction and maintenance of large float glass furnaces during production and operation are directly related to the short-term and long-term benefits of float glass enterprises. The main reason for the cold repair of most domestic glass furnaces is the serious burning of the glass furnace side wall. Therefore, the correct design and maintenance of the glass furnace side wall is one of the keys to extend the service life of the furnace and thus increase production and economic benefits. Now we will exchange ideas on a domestic glass furnace with a melting capacity of 700 t/d and 7 pairs of ports, which is mainly designed according to foreign technology.
1. Design features of 700t/d glass furnace side wall
2. Importance of Melting Process Control to Side Wall Maintenance
1.Design features of 700t/d glass furnace side wall
1.1 Design Basis
The side wall of the glass melting furnace is the area where the batch material is melted into qualified glass liquid and is in direct contact with the glass liquid. The operating temperature range is generally 1200~1600℃. The contact area between the inner surface of the side wall and the surface of the glass liquid is affected by the combustion of fuel, the melting of batch material, the scouring and alteration of the glass liquid flow, and the fluctuation of the liquid level.
Therefore, the erosion of the side wall is relatively serious, especially the side wall near the glass liquid surface linve a certain degree of shock resistance and low thermal conductivity. The ideal material for the side wall of the glass melting furnace is fused cast zirconium corundum block(fused cast AZS block), and the high-temperature erosion resistance of fused cast zirconium corundum block increases with the increase of ZrO2 content.
At present, the side wall of large domestic float glass furnaces is made of large blocks with vertical seams and dry masonry. The material is generally fused cast AZS 33# blocks and fused cast AZS 36# blocks. Fused cast AZS 41# blocks have poor thermal stability and are prone to cracking during glass furnace heating up. They are also expensive and are rarely used. In order to extend the service life of the side wall blocks, forced cooling of the side wall blocks at the liquid level is often used, that is, cooling by blowing cooling air and water.
1.2 Material selection requirements
Based on the positioning of the float glass melting furnace to produce glass products, select the refractory material supplier and put forward quality requirements. The design age of this glass furnace is 10 years. The melting part side wall blocks are selected from Beijing Xipu as the manufacturer.The feeding zone and the melting zone both use oxidation method fused cast AZS 36# WS blocks, and the 4 sidewall blocks on the left and right sides of the hot spot area and the corner sidewall blocks entering the neck use oxidation method fused cast AZS 41# WS blocks.
1.3 Size requirements
The thickness of the side wall blocks in the melting part of the glass melting furnace is 250mm, the height is 1330mm (30mm lower after the clarification part), and the width is 400mm (the outer side and the lower part are the casting mouth). When installing, use a whole large block to lay it vertically. During normal production, the height of the side wall above the glass liquid level in the melting part is 70mm, and a 300mm height is reserved on the outside of the side wall without insulation. A 600mm high block patching position is reserved near the glass liquid level line for external cooling by blowing air.
2. Importance of Melting Process Control to Side Wall Maintenance
(1) When formulating melting process indicators, the maintenance of the glass furnace must be taken into consideration.
For example, the moisture control of the batch entering the glass furnace, the melting temperature control, the length and inclination angle control of the flame, and the glass liquid level control, especially in the first and second block patching half a year and at the end of the melting furnace, the glass liquid level can be appropriately lowered in stages and the upper end of the sidewall can be strengthened to appropriately extend the glass furnace life.
(2) When determining the liquid level, it is essential to take account of the material pile at the front end of the furnace, the flux in the batch and the foam generated in the molten state will increase the ablation of the upper end of the sidewall (the height of the sidewall blocks corresponding to the first three pairs of ports should be considered, which should be increased by about 40mm)
3.1 The blowing position of the air nozzle
One of the factors to extend the service life of the glass furnace side wall is to choose the appropriate blowing position of the air nozzle.
Pay attention to the observation of the side wall condition of the glass furnace after the glass liquid is released during normal production and cold repair. The blowing position of the air nozzle should be determined according to the height of the glass liquid level and foam in the glass furnace. According to industry experience,
▶️ In fact, the viscosity of the glass liquid in the furnace (including the pile of materials in the early stage of melting and the foam before the hot spot) makes the glass liquid level gradually decrease from the front end of the furnace tank to the 4th port along the longitudinal direction of the furnace.
The installed air nozzle should also be higher in the front and lower in the back with the change of the liquid level in the furnace,
1️⃣ that is, the liquid level from the front end doghouse to the 2nd port is 30~50mm higher than the actual liquid level, and the corresponding air nozzle blowing position is 30~70mm away from the upper edge of the side wall.
2️⃣ The corresponding air nozzle blowing position of the 2nd to 4th ports should be gradually reduced from 30~70mm away from the upper edge of the side wall to 50~90mm.
3️⃣ The front and back of the 5th ports are the most active areas of glass liquid flow. The viscosity of the glass liquid is small, and the scouring and high-temperature ablation of the sidewall are more serious. The corresponding air nozzle blowing position should be in the area of 70~120mm away from the upper edge of the sidewall, and all air nozzles are 30° upward at an angle to the horizontal.
3.2 Air volume of air nozzles
1️⃣ it should be adjusted according to the distribution of batch materials in the furnace, the glass liquid flow conditions and the regional fuel spray gun settings, rather than using the same air volume from front to back;
2️⃣ according to the different periods of furnace operation, the total air volume and the air volume of each regional segment should also be adjusted according to the actual situation, rather than keeping the entire furnace unchanged or the air volume of each region the same. The air volume is the largest in the area with the most serious ablation trend, in order to synchronize the ablation of the entire side wall.
(1) Adjustment of air volume in each area
① Under the premise that the blowing position of the cooling air nozzle of the sidewall is correct, the oil consumption of the #2 port is large and the material temperature is high. At the same time, the dispersion of soda ash in the batch is also serious, which makes the sidewall in this
② The convection of the glass liquid in the #4~6 port area has a large impact on the sidewall, so the air volume is also large (the air valve opening is 75%~85%);
③ The sidewall erosion in the #1 and #3 port areas is slightly more serious, and the air valve opening is 70%~80%
④ The air valve opening corresponding to the sidewall in other areas gradually decreases from 60%~70% of the #7 port to 40% later.
(2) Adjustment of total air volume in each operation period and the slight adjustment of air volume in each area
① In the first and second years of furnace operation, the total air volume reaches 60%~70% of the design air volume, and the air volume in each area is slightly different;
② In the third and fourth years of furnace operation, the total air volume reaches 80%~90% of the design air volume, and the air volume in each area is close to the requirements of (1) above;
③ In the fifth and sixth years of furnace operation (i.e. before the first brick patching), the total air volume reaches 90%~100% of the design air volume, and the air volume in each area meets the requirements of (1) above, and the air volume in areas with particularly serious burnout can reach 95%;
④ In the sixth year of furnace operation (i.e. after the first brick patching of the sidewall), the total air volume and the air volume in each area can be adjusted back to the third year state before brick patching, and the continuity of the junction where bricks are not patched is maintained. Then gradually adjust the total air volume and the air volume in each area until the furnace is operated until the second brick patching of the sidewall or the end of the furnace service life.
Summary
Correct maintenance of the furnace sidewall is the key to ensuring long-term stable operation of the glass furnace, extending the furnace service life and improving production efficiency.
►The design features of the 700t/d melting furnace side wall include the design basis based on the furnace capacity, material durability and thermal stress management, the selection of high temperature resistant and corrosion resistant materials to meet the material selection requirements in harsh working environments, and the selection of materials based on the furnace structure. Dimensional requirements accurately set by process requirements together form a solid foundation for side wall design.
►Melting process control is crucial to the maintenance of the side wall. Reasonable temperature gradient, stable melting state and optimized glass flow can significantly reduce erosion and wear of the side wall.
►In addition, the correct selection of the blowing position and air volume of the furnace side wall cooling nozzle, through precise air volume distribution and blowing position adjustment, can achieve effective cooling of the side wall, prevent the cracking of the side wall bricks caused by thermal stress, and further extend the furnace service life.
In summary, through comprehensive design, material selection, process control and reasonable configuration of cooling nozzles, the furnace side wall can be effectively maintained, the stability and service life of the glass furnace can be improved, and production efficiency can be increased.
Henan SNR Refractory Co., Ltd. has been specializing in the production of fused cast AZS blocks for about 25 years. We use high-quality raw materials and advanced fusion technology to provide customers with high-quality products. From raw material procurement to finished product delivery, every step is strictly quality inspected to ensure that every indicator meets the standards, so you can use it with confidence.
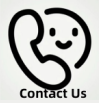
If you have any needs, you can contact me at any time.
Web:www.snr-azs.com
Email:wendy@snrefractory.com