To extend the operational cycle of glass furnaces, it is essential to improve or enhance the quality of refractory materials used in glass furnaces to meet the demands of the modern glass industry.
Fused cast AZS refractory materials are used in various critical parts of glass furnaces. By refining and improving the quality of Fused cast AZS refractory products, we can address and resolve issues that arise during the operation of glass furnaces. Various accidents in glass furnaces cause significant economic losses to glass manufacturers. These accidents can be attributed to furnace aging, improper furnace operation processes, operational errors, and the quality of refractory materials. Statistical analysis of glass furnace leakage accidents reveals that over 60% of such incidents are caused by leaks in the furnace bottom. Therefore, improving the quality of Fused cast AZS paving blocks for glass furnace bottoms is a crucial step in extending the service life of glass furnaces.
1. Production Process of Fused cast AZS Blocks
2. Production Method of Fused cast AZS Paving Blocks Before Improvement
3. Production Method of Fused cast AZS Paving blocks After Improvement
4. Conclusion
1. Production Process of Fused cast AZS Blocks
Fused cast AZS blocks are produced by melting industrial alumina powder and zircon sand (containing approximately 66% zirconia and 34% silica) in an electric furnace at high temperatures (melting temperature between 1,780°C and 1,840°C). The molten material is then cast into molds and cooled to form a nearly white solid. The mineralogical structure of the blocks consists of a eutectic of corundum and zirconia, along with a glass phase that fills the spaces between the crystalline structures.
►After the casting process, the outer parts of the product, which are in contact with the mold, solidify quickly, while the center remains in a liquid state. Over time, the product solidifies from the outside inward until it is completely solid.
►The annealing process involves the transition from a liquid to a solid state, during which internal stresses are gradually relieved. When the product is largely in a liquid state within the mold, it aids in the formation of crystal structures, the feeding of molten material into the block, and the diffusion of thermal stresses. The diffusion of thermal stresses in the liquid state helps reduce cracking in the product.
Therefore, extending the time the material remains in a liquid state within the mold is a critical factor in improving the product‘s bulk density and forming rate.
2. Production Method of Fused cast AZS Paving Blocks Before Improvement
Currently, the production method of Fused cast AZS paving blocks in the industry is relatively traditional and mainly involves three steps: mold assembly, casting and venting, and heat preservation and unloading. Below is a detailed description of each step.
2.1 Mold Assembly
In the pre-improvement production method, mold assembly is the first step in the production process.
As shown in Figure, the paving block molds are arranged in a heat preservation box according to specified intervals. Each heat preservation box is generally of similar size and can accommodate four paving blocks. Each block has a casting riser positioned above the mold for subsequent casting and feeding operations.
When arranging the molds, a certain distance must be maintained between the products to ensure that each block is evenly heated and cooled during the casting process. After assembly, the heat preservation box is filled with heat preservation materials, whose main function is to slow down the cooling rate of the blocks, preventing cracking or internal stress concentration caused by rapid cooling. Once the heat preservation materials are filled, the box is ready for casting.
2.2 Casting and Venting
Casting is a critical step in the production of Fused cast AZS paving blocks. After the melting process is completed according to the prescribed procedure, the heat preservation box is moved four times to complete the casting of the four paving blocks. Each time the box is moved, the molten Fused cast AZS material is poured into the mold through the casting riser, forming the preliminary structure of the block.
After casting, the hardened shell on the surface of the casting riser is broken at the specified time. This step allows the molten material in the riser to continue feeding into the block, thereby increasing the product‘s bulk density and eliminating porosity in the block‘s cross-section. The feeding process is crucial for improving the block‘s density and mechanical strength, as porous blocks are prone to cracking or damage in high-temperature environments.
2.3 Heat Preservation and Unloading
After casting and venting, the products in the heat preservation box enter the heat preservation stage. In the box, a layer of heat preservation material is placed over the casting risers, with a thickness generally not exceeding 100 mm. The heat preservation material further slows down the cooling rate of the blocks, ensuring that they solidify evenly from the outside inward and avoiding internal stress caused by uneven cooling.
The box is then transferred to the heat preservation area. The heat preservation period typically lasts six days, during which the blocks gradually transition from a liquid to a solid state, and internal stresses are gradually relieved. After heat preservation, the surface temperature of the products drops to room temperature, and the blocks can be unloaded. After unloading, the blocks proceed to subsequent processing or inspection stages.
2.4 Issues with the Pre-Improvement Production Method
Although this traditional production method can produce qualified Fused cast AZS paving blocks, it still has some issues:
► Low Production Efficiency: Since each casting requires moving the heat preservation box four times, and the casting and feeding processes for each block are relatively independent, production efficiency is low.
► Unstable block Quality: Due to the limited thickness of the heat preservation material, the blocks may cool too quickly in certain areas during the cooling process, leading to uneven internal stress distribution and potential cracking or porosity.
► High Energy Consumption: The traditional production method requires a long heat preservation time, and the heat preservation effect is not ideal, resulting in high energy consumption.
3. Production Method of Fused cast AZS Paving blocks After Improvement
After the improvement, the arrangement of Fused cast AZS paving blocks in the heat preservation box is shown in Figures.
3.1 Mold Assembly
As shown in Figures, a connected mold assembly method is adopted. The number of molds assembled depends on the size of the heat preservation box. After assembly, the molds are placed together in the heat preservation box, with the wide faces of the molds tightly connected and neatly arranged. Based on the size of the heat preservation box, a fixed number of paving blocks are assembled each time. The size of the casting riser is determined according to the overall specifications of the assembled molds and is placed above the block molds. After assembly, a 200 mm space is left around the molds for filling with heat preservation materials.
This improved assembly method offers several advantages: First, the blocks are tightly connected, allowing for better heat transfer and providing the best heat preservation effect. The material remains in a liquid state for a longer time within the mold, facilitating the diffusion and release of thermal stresses and reducing the risk of cracking. Second, the extended liquid state makes it easier for the molten material in the riser to feed into the block, increasing the product‘s bulk density and improving its quality. Third, the casting process is accelerated, aiding in extending the liquid state and improving production efficiency.
3.2 Casting and Venting
After the melting process is completed according to the prescribed procedure, the casting of multiple paving blocks in the heat preservation box is completed in one go. Due to the significantly enlarged casting riser after the improvement, casting becomes easier, and the casting speed is noticeably increased, reaching 25 to 28 kg/s. Three minutes after casting, the first venting is performed by breaking the surface of the riser with a steel rod and inserting it halfway into the block. This process is repeated every three minutes, with the rod inserted deeper each time, for a total of three venting cycles. This venting method ensures that the molten material in the riser adequately feeds into the block, resulting in a final product free of porosity and with increased bulk density.
3.3 Heat Preservation and Unloading
Before transferring to the heat preservation area, a heat preservation layer of at least 200 mm is placed over the casting riser, with the heat preservation effect of the riser and its upper part being superior to that of the lower part. The heat preservation period is extended to eight days, and the blocks are unloaded when the surface temperature reaches around 40°C.
The heat preservation method is a critical step. Due to the connected assembly method, the heat transfer between the blocks ensures excellent heat preservation. Therefore, special attention is paid to the heat preservation of the riser and its upper part to ensure that the material remains in a liquid state for a sufficient time to allow for adequate feeding. If the heat preservation effect above the riser is poor, the molten material in the riser will solidify prematurely, leading to insufficient feeding and resulting in large-area collapse or porosity in the block‘s cross-section. From a comparative perspective, with the same heat preservation time of seven days, the surface temperature of the improved paving blocks is much higher than that of the pre-improvement blocks, meaning the unloading time for the improved blocks must be extended by one day to meet the required temperature.
Through the improvement of the production process for Fused cast AZS paving blocks, the quality and production efficiency of the products have been significantly enhanced. The pre-improvement production method involved individual casting, while the improved method adopts connected casting. This improvement not only optimizes the production process but also brings multiple benefits.
4.1 Advantages of Connected Casting
The connected casting method is particularly suitable for paving blocks with conventional thicknesses of 75 mm, 100 mm, and 120 mm. Compared to individual casting, connected casting offers the following significant advantages:
►Improved Production Efficiency: Connected casting completes the casting of multiple blocksin one go, reducing the number of times the heat preservation box needs to be moved, significantly shortening the production cycle, and improving production efficiency.
► Optimized Heat Preservation Effect: The tight connection between the blocks allows for more uniform heat transfer, significantly enhancing the heat preservation effect. The material remains in a liquid state for a longer time within the mold, facilitating the diffusion of thermal stresses and reducing the risk of cracking.
► Enhanced Product Quality: The extended liquid state allows the molten material in the riser to fully feed into the block, increasing the product‘s bulk density and improving its density and mechanical strength.
4.2 Increase in Bulk Density
Before the improvement, the bulk density of Fused cast AZS paving blocks ranged from 3.65 to 3.70, while after the improvement, it reached ≥3.70. This increase not only enhances the block‘s compressive strength and thermal shock resistance but also significantly improves its stability in high-temperature environments. The increase in bulk density directly reflects the densification of the block‘s internal structure, reducing porosity and improving its service life.
4.3 Economic Benefits
The improved production method not only enhances product quality but also brings significant economic benefits:
► Increased Yield Rate: By optimizing the casting and heat preservation processes, the yield rate has increased by 5% to 10%, reducing the scrap rate and lowering production costs.
► Reduced Molten Material in Riser: The improved design of the casting riser has reduced the amount of molten material in the riser by 8% to 10%, further saving raw materials.
► Enhanced Market Competitiveness: The improvement in product quality and reduction in production costs have made Fused cast AZS paving blocks more competitive in the market, better meeting customer demands.
4.4 Impact on Glass Furnace Operation
For Fused cast AZS paving blocks of the same specifications used in glass furnace bottoms, the improved product represents a significant upgrade in quality. The high bulk density and excellent thermal shock resistance of the blocks ensure stable performance in the high-temperature environment of glass furnaces, reducing furnace leakage accidents caused by block damage. This not only improves the continuity and stability of glass production but also lays a solid foundation for extending the service life of glass furnaces.
Henan SNR Refractory Co., Ltd. has been specializing in the production of fused cast AZS blocks for about 25 years. We use high-quality raw materials and advanced fusion technology to provide customers with high-quality products. From raw material procurement to finished product delivery, every step is strictly quality inspected to ensure that every indicator meets the standards, so you can use it with confidence.
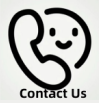
If you have any needs, you can contact me at any time.
Web:www.snr-azs.com
Email:wendy@snrefractory.com