In the glass manufacturing industry, even for the same glass products and the same glass furnaces, the maintenance time, repair locations, and furnace service life can vary significantly. Normal material erosion falls within the designed service life range, while abnormal material erosion refers to malignant conditions that occur at uncertain locations and within the designed service life of the material. These conditions have significant hidden negative effects, impacting not only the economic interests of glass enterprises but also, to some extent, hindering the healthy development of the entire glass industry.
1. Harmful Components Inevitably Present in Fused Cast AZS Products and Their Erosion Mechanisms
2. Entry of Harmful Components During the Production of Fused Cast AZS Products
3. Formation of Gaps in Glass Furnaces
1. Harmful Components Inevitably Present in Fused Cast AZS Products and Their Erosion Mechanisms
1.1 Glass Phase
The phase composition of fused zirconia corundum refractory products (AZS) includes zirconia, corundum, a small amount of mullite, glass phase, and pores. During the manufacturing process of fused zirconia corundum bricks, a certain amount of glass phase is required to act as a buffer to absorb thermal stress and reduce residual thermal stress. However, the presence of the glass phase also brings some disadvantages. In terms of the refractory material‘s resistance to glass melt erosion, the glass phase is the weak link. During the erosion process, the glass phase is first extracted and exchanged with the high-temperature glass melt, thereby accelerating the erosion of the crystals. Under high-temperature operating conditions, the glass phase can also seep out, accompanied by the release of bubbles, which contaminates the glass melt.
1.2 Carbon Infiltration
Fused zirconia corundum bricks produced by the general reduction method often have severe carbon infiltration. According to literature reports, the carbon content can be judged by the color of the refractory material‘s cross-section:
- light gray (0.03%~0.06%),
- gray-white (<0.03%),
- gray (0.08%~0.18%),
- dark gray (0.15%~0.19%).
Even products produced by advanced oxidation methods (long arc and oxygen blowing) contain some carbon (<0.01%). Carbon infiltration exists in the form of carbides, nitrides, sulfides, solid carbon, and residual reducing gases. When used under oxidizing conditions, these components release gases, causing the temperature at which the glass phase seeps out to decrease. When AZS products contain a higher glass phase (generally around 20%), it will soften and seep out at temperatures above 1,100°C, with the loss intensifying as the temperature rises. The seepage of the glass phase is related to the presence of carbon, carbides, and low-valent iron and titanium impurities in the bricks.
2. Entry of Harmful Components During the Production of Fused Cast AZS Products
2.1 Sand Inclusion and Other Foreign Matter Entering the Product
Sand inclusion in quartz sand and water glass-based casting models
Sand inclusion refers to a phenomenon similar to that occurring in AZS sidewall block casting, where the high-temperature melt gradually rises in the mold. The part not covered by the melt is exposed to high temperatures, causing the surface sand to detach in chunks and fall into the melt, resulting in sand inclusion. Figure 1a shows the localized detachment of the quartz sand mold‘s surface layer due to high temperatures during casting, falling into the melt. Figure 1b illustrates the internal sand inclusion in the product, where the added sand, after being subjected to 1,750°C high temperatures, exists in a glassy state within the product.
Additionally, during the melting process, there is a leveling procedure using a cast steel rod as the leveling tool. Prolonged exposure of the steel rod to high-temperature melts can soften its texture, leading to breakage when prying unmelted material blocks. The broken rod in the melt may either completely melt, increasing the iron content in the product, or remain partially unmelted and enter the product during casting, as shown in Figure 1c.
2.2 Oxidation Uniformity of Fused Cast AZS Products
The degree or uniformity of oxidation in fused cast AZS products is one of the key indicators of product quality. While manufacturers have well-established requirements for oxygen blowing processes, most have deficiencies in oxygen lance positioning.
As shown in Figure 2, oxygen lance nozzle clogging is an unavoidable phenomenon during oxygen blowing. Typically, an oxygen lance has seven oxygen outlets distributed around or at the bottom of the ball head.
When one or several outlets are clogged, the oxidation uniformity of the product is compromised. Severe cases are visually detectable, while minor cases are not easily discernible. Even within a single brick, color inconsistency may occur, with darker colors indicating higher carbon infiltration and lighter colors indicating lower carbon infiltration. Clogging of the oxygen lance nozzles directly leads to poor oxidation effects and increased carbon infiltration in the product. During glass furnace operation, the glass phase often precipitates alongside bubbles, mostly carbon dioxide gas.
3. Formation of Gaps in Glass Furnaces
3.1 Grinding Processing or Furnace Construction
During the grinding and processing of products, the aging of the machine bed surface can lead to insufficient flatness, causing the product‘s surface to bulge or concave in the middle. During pre-assembly, the gaps are evenly distributed, making them appear small. However, during furnace construction, errors in the foundation‘s flatness or defects in the product‘s base, combined with the negligence of workers, can result in the product being suspended at the bottom. During the glass furnace heating process, the product‘s expansion may not follow the evenly distributed gaps, potentially causing significant widening of gaps at the bottom or top of the sidewall bricks, as shown in Figures 3 and 4.
3.2 Design of Glass Furnace Weir Specifications
In glass furnaces, improper arrangement of weir bricks can lead to deformation due to the impact of the glass melt. Since weir bricks must withstand the impact force of the flowing glass melt, they require sufficient thickness and support. As shown in Figures 5 and 6 (arrows indicate the direction of glass melt flow), the support bricks should exceed half the height of the weir bricks to provide effective support. When weir bricks deform under the impact of the glass melt, the gaps between the bricks widen.
3.3 Furnace Deformation
Within the temperature range of furnace heating, the zirconium component in fused cast AZS products undergoes a phase transformation from monoclinic to tetragonal at 1,100°C, accompanied by volume changes. Temperature fluctuations can cause reverse volume changes, which are the root cause of product cracking. During glass furnace heating, a holding stage is typically set at 1,100°C to allow sufficient volume transformation of fused cast AZS products.
4.1 Viscosity and Temperature of the Glass Melt
Higher furnace temperatures result in lower viscosity of the glass melt. Elevated process temperatures in glass furnaces are required for certain factors (e.g., oxy-fuel combustion technology, ultra-clear glass, etc.). Appropriately increasing the glass melting temperature can improve melting efficiency, reduce glass melt viscosity, and facilitate bubble removal. While lower viscosity benefits glass quality, it adversely affects the erosion resistance of sidewall bricks, particularly in terms of gap erosion, which is considered abnormal erosion. Low viscosity allows the glass melt to easily penetrate brick gaps, and the upward movement of bubbles and the friction caused by the mechanical movement of the glass liquid further aggravate the erosion of the brick joints. This is the root cause of abnormal gap erosion, emphasizing the importance of minimizing gaps.
4.2 Abnormal Erosion of Vertical Gaps in Sidewalls
During glass furnace operation, the glass melt penetrates oversized brick gaps. In this environment, the upward mechanical movement of the glass melt, along with the precipitated glass phase and bubbles, intensifies gap erosion. In addition, the flow of glass liquid has a backflow effect at the gap. This backflow effect is a mechanical flow scouring process, which will make the brick joints larger and larger. This is one of the abnormal erosion states, as shown in Figures 7 and 8. Figure 9 also shows abnormal erosion of the vertical joints of the sidewall.
4.3 Abnormal Erosion at the Glass Line of Sidewall Bricks
When the product contains a high glass phase content, inferior product quality with excessive impurities can result in sodium content exceeding 2%. During glass furnace operation, the glass phase precipitates extensively, and the liquid friction between the glass melt and the precipitated glass phase accelerates erosion. At the triple-phase boundary, the erosion rate is extremely fast. For example, some glass furnaces designed for a 5-year lifespan experience complete erosion of the upper 300 mm of the sidewall in less than 2 years. This is a typical abnormal erosion phenomenon, as shown in Figure 10a. Other erosion factors have been extensively reported in the literature and are not repeated here.
4.4 Vertical Gap Erosion in Weir Bricks
When weir bricks deform under the impact of the glass melt, the gaps between the bricks widen. These widened gaps provide space for the glass melt, and the upward friction between the precipitated glass phase and the liquid glass melt leads to abnormal erosion of the weir bricks. As shown in the middle of Figure 10b, the weir bricks show a jagged shape due to abnormal erosion.
4.5 Factors Contributing to Hole Erosion in Sidewalls
(1) The presence of foreign objects such as iron rods in the product. Iron, containing over 2% carbon, is a harmful substance that accelerates product erosion and negatively impacts glass quality.
(2) Sand inclusion within the product, particularly concentrated areas, as shown in Figure 10c.
(3) Uneven oxidation due to clogged oxygen lance nozzles, resulting in high carbon infiltration. When gaps are present, the precipitation of the glass phase accompanied by bubbles exacerbates localized abnormal erosion.
(4) When cross-edge cracks or local cracks of the product and a large amount of carburization converge together, the reflux erosion of the glass liquid and the excessive glass phase content cause the precipitation of a large amount of glass phase accompanied by bubbles, leading to the drilling erosion shown in Figure 9, or even a glass melt leakage accident.
(1) The glass liquid is seamless. The gaps between products will cause mechanical erosion by the glass liquid backflow. When the glass is separated from the gap, bubbles will be separated, which will aggravate the erosion of the product gap. When the glass furnace is inspected as a whole, the stricter the requirements for the gap, the better.
(2) When the glass furnace is built, ensure that the foundation is stable, there should be no product overhead, the expansion joints should be reasonably reserved, or the masonry personnel should strictly control the business.
(3) Increase the height and width specifications of the inner protective bricks for weir bricks. Ensure the protective bricks provide effective support.
(4) Implement effective management systems to monitor oxygen lance nozzle clogging during the production of fused cast AZS products. Position oxygen lances for easy observation of nozzle conditions.
(5) For quartz sand and water glass-based molds, the water glass ratio should not be less than 8%. Insufficient water glass can cause surface sand detachment during casting, introducing internal defects. Resin sand molds are preferred for producing fused cast AZS products.
Henan SNR Refractory Co., Ltd. has been specializing in the production of fused cast AZS blocks for about 25 years. We use high-quality raw materials and advanced fusion technology to provide customers with high-quality products. From raw material procurement to finished product delivery, every step is strictly quality inspected to ensure that every indicator meets the standards, so you can use it with confidence.
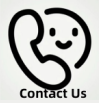
If you have any needs, you can contact me at any time.
Web:www.snr-azs.com