Melting quality is crucial for ensuring the quality of glass products. The requirements for melting and homogenization vary depending on the type of glass produced. For general container glass, the product meets quality standards as long as it is free from cracks, has minimal residual stress, and maintains accurate dimensions. A limited number of defects such as bubbles and stones are permissible, provided their size and quantity comply with the company’s internal quality control standards. The demand for melting uniformity is relatively lenient.
However, the bottle glass industry faces intense competition, where product quality directly impacts market competitiveness. To enhance quality, manufacturers must improve melting and homogenization performance. High-end glass products impose strict requirements on striations, stones, dense bubbles, and melting uniformity—sometimes even exceeding the standards for optical glass.
Compared to flat glass furnaces, daily-use glassware production lines typically operate on a smaller scale, with most utilizing end-fired furnaces. Therefore, while quality control methods share similarities with those of other glass manufacturers, adjustments must be made to accommodate the specific furnace type.
1. Improving Batch Preparation Quality
2. Control of Fuel Stability
3. Glass Melting Regime
1. Improving Batch Preparation Quality
Glass production requires four key stabilities: raw material stability, fuel stability, melting stability and forming stability. Among these, raw material stability is the primary one. The glass furnace serves as a molten liquid mixer while the mixing equipment functions as a solid mixer. It can be said that batch quality and glass melting quality each account for half of the product quality impact. Improving batch quality is the prerequisite for enhancing melting quality. To ensure stable batch quality, the following measures must be implemented:
(1) Strict quality control of incoming raw materials: Strengthen storage and usage management of raw materials. Substandard materials must not be used in production.
(2) Stable operation of batching system: Ensure weighing, mixing and conveying equipment meet performance requirements. Enhance equipment maintenance and routine inspections to prevent operational abnormalities. Strictly control static and dynamic weighing accuracy in the batching system. The production processes of weighing, mixing and conveying must meet technical requirements. Establish proper raw material mixing sequences and strictly implement batch uniformity testing and assessment - this is a crucial step in improving batch quality.
(3) Formula optimization: The formulated batch should consider both cost and melting performance, specifically the total melting time. Formulas with shorter melting and clarification times can reduce melting temperature and increase melting rate. Without affecting product performance, appropriately adjust glass composition to further optimize formulas, improve melting rate and enhance melting quality.
(4) Strict particle size distribution control: The most critical control is for aluminosilicate raw materials. Silicate formation only accounts for 9-13% of total melting time, while dissolution of refractory quartz particles takes 87-91%. Overly coarse silica particles are difficult to melt, while excessively fine particles tend to form lumps that are hard to mix uniformly. Moreover, overly fine particles generate micro-bubbles during melting, making clarification difficult and prolonging clarification time. In severe cases, "starry sky" bubble defects may appear in products. For quartz sand, over 90% should be 0.25-0.38mm (40-60 mesh), with all particles passing 0.83mm (20 mesh), and particles below 0.109mm (140 mesh) not exceeding 5%. In northern regions, prevent moisture-containing quartz sand from freezing in winter by sieving before use when necessary.
(5) Appropriate increase of cullet ratio:
Adding certain proportion of cullet as flux during melting can accelerate batch melting and improve melting rate. The ideal cullet ratio is about 30%. However, the amount of cullet generated during production is relatively low, usually not exceeding 10% of total feed, so purchasing low-cost waste glass products can reduce raw material costs. But ensure purchased cullet meets quality standards to guarantee melting quality.
(6) Using glass physicochemical properties for production control: In glass production, stable composition is crucial for improving product quality. Currently, the precision in raw material preparation, weighing, mixing and conveying is not ideal, mostly in unstable states, and control over composition fluctuation is inadequate. Relying solely on traditional volumetric analysis for composition testing cannot provide timely and effective production control. Using physical property measurements for production control is essential. Advanced countries commonly monitor glass properties like thermal expansion coefficient, density and softening point (Ts) for production control. Glass system engineering software can quickly and accurately analyze sample composition, compare with formulas in time, and implement targeted adjustments to stabilize and improve production quality.
(7) Using glass COD value for clarification control: Glass clarification is critical for improving melting quality. Calculate batch Redox number using raw material COD values, determine Redox value by measuring Fe2+/Fe3+ ratio in glass, and use Redox value for oxidation-reduction control to ensure stable and improved clarification quality.
2. Control of Fuel Stability
2.1 Implementation of National Environmental Policies
Glass enterprises are major energy consumers. Fuels such as natural gas, heavy oil, coal tar, coke oven gas, producer gas, and petroleum coke powder have been successfully used in China‘s glass furnaces, making significant contributions to the development of the glass industry. In recent years, the government has imposed increasingly stringent environmental requirements, urging enterprises to save energy and reduce emissions. Measures have been taken to restrict highly polluting fuels, leading to the shutdown or renovation of glass enterprises that primarily use coal gas. To comply with national energy-saving and environmental policies, it is imperative to upgrade glass furnaces and production lines for energy efficiency and environmental protection.
Natural gas is a high-quality energy source that is colorless, odorless, non-toxic, high in calorific value, stable in combustion, and environmentally friendly. Its main component is methane (CH₄), along with certain amounts of ethane and propane, and it contains no carbon monoxide, making it a relatively safe fuel. When natural gas resources are available, glass enterprises should prioritize its use as the primary fuel for production. Collaboration with research institutions and professional energy-saving technology companies is essential to adopt advanced natural gas energy-saving technologies, reduce furnace fuel consumption, and implement flue gas desulfurization, denitrification, and dust removal. Equipping furnaces with online automatic flue gas monitoring devices ensures compliance with emission standards.
Stable fuel supply must be ensured to maintain continuous and safe glass production. In terms of quality, natural gas should ideally have a calorific value of 35,580–39,750 kJ/m³ and a total sulfur content of <200 mg/m³. During use, it is crucial to ensure the calorific value meets process requirements, with stable pressure and flow rates, and regular calorific value testing.
Glass furnaces aim for "three highs and two lows" during production: high output, high quality, long service life, low energy consumption, and low pollution. A scientific and comprehensive automatic control system is essential. The design of the furnace‘s automatic control system must fully consider environmental factors, furnace structure, and production process requirements, with the flexibility to adapt to process adjustments. The goal is to improve melting quality, achieve high product quality and output, and meet energy-saving and environmental standards.
2.2 Flame Control Requirements for End-Fired Glass Furnaces
Melting operations play a critical role in ensuring furnace stability and improving melting quality. Operators must regularly inspect the length, height, rigidity, and brightness changes of the flames in the ports. If the flames appear unstable (e.g., "floating"), the furnace temperature readings may be falsely high, leading to unstable melting conditions.
The highest temperature should be maintained within 1.2–1.8 m at the end of the melting zone flame, close to the batch pile, and controlled within the feeding and majority melting areas. The hotspot should be positioned within 2/3 of the furnace length, and the foam line should be maintained between 1/2 and 2/3 of the furnace length. Proper control of the hotspot accelerates glass flow and circulation, ensures a distinct foam line, and improves thermal efficiency, resulting in significant energy savings.
By using specialized DCS furnace control software, flame control can shift from experience-based to scientific methods. The software enables effective collection of furnace thermal parameters and controls the combustion system, temperature distribution, furnace pressure, glass level, and flue draft. Since furnace reversal significantly impacts operational conditions, the software must meet flame reversal requirements based on time and temperature composite commands, thereby improving thermal efficiency and furnace lifespan.
3. Glass Melting Regime
3.1 Observation and Control of Melting End Temperature
A radiation pyrometer is installed at the observation hole on the side wall opposite the charging end to monitor flame combustion status and batch melting effect. Radiation pyrometers are installed at middle-rear observation holes on both sides of the melting end to observe glass clarification and homogenization processes. Thermocouple temperature measurement devices are installed at the crown positions of 1/2 and 2/3 along the furnace length as temperature monitoring points for the entire furnace.
Operators should regularly observe flame shape, brightness of sidewall blocks and silica crown bricks, and foam line position through observation holes. The foam line position generally should not exceed 2/3 of the total furnace length. Periodic manual measurements using handheld radiation thermometers through observation holes should be conducted for comprehensive temperature analysis.
In daily glass production, order changes may require product transitions, which affect pull rate and glass temperature, consequently altering the furnace temperature regime. Similarly, replacement of feeder refractories or forming equipment failures causing glass diversion will also impact the temperature regime. Significant temperature fluctuations occur especially when furnace or raw material abnormalities happen.
Changes in the furnace temperature regime cause variations in hotspot and foam line positions, leading to substantial temperature fluctuations at the forehearth that result in unstable forming and increased product defects. Severe cases may alter glass flow speed and direction. Simultaneously, bottom temperature changes affect the thickness of the "static layer", allowing static layer glass to enter the forming flow, increasing glass inhomogeneity and causing product streaks or cracks. When such changes occur, immediate adjustment of the temperature regime is necessary to stabilize hotspot temperature and foam line position.
3.2 Temperature Regime of Melting End
Melting temperature is a critical operational parameter in glass melting, where fluctuations significantly impact hotspot and foam line stability. As end-fired furnaces use alternating burner groups, longitudinal temperature curves tend to fluctuate, requiring frequent observation and adjustment. Stable and consistent operation should be maintained through regenerator reversal.
A proper temperature regime along the furnace length must be established in the process specification. For end-fired furnaces, the most crucial parameters are hotspot temperature and position. Only when hotspot temperature is prominent and both its value and position meet requirements can an ideal foam line be formed. The hotspot temperature value depends on glass type, fuel type, and refractory quality.
By adjusting combustion air/fuel ratio at the ports, flame length, brightness and rigidity can be optimized to achieve ideal combustion conditions with prominent hotspot temperature and proper horizontal temperature profile. Continuous monitoring and control of flue gas composition should be implemented to adjust combustion air and fuel flow rates timely, achieving optimal air/fuel ratio and improving heat transfer efficiency.
Through proper temperature profile, various solid batch materials are transformed into a single, homogeneous glass phase, with visible bubbles eliminated through clarification. Glass melting consists of five stages:
1.Silicate formation (800-900°C, batch transforms into opaque sintered silicates and silica)
2.Glass formation (1200-1250°C, sintered material melts into glass)
3.Refining (1400-1500°C, gas release from molten glass)
4.Homogenization (extended high temperature treatment for chemical uniformity)
5.Cooling and forming (1350-1420°C after refining/homogenization)
When batch pile, foam line, refining zone and mirror zone all meet process requirements, high-quality molten glass can flow through the throat to forming.
In furnace automatic control systems, fuel-based temperature automatic control is a reliable method for maintaining stable melting temperatures during normal operation. The system automatically adjusts fuel and combustion air flows to maintain stable temperatures measured by crown thermocouples. Typically three crown thermocouples are installed, whose signals can be proportionally combined as the control temperature. The proportion factors can be adjusted based on actual conditions. If one thermocouple fails, the system can still maintain effective temperature control through proportional adjustment.
3.3 Foam Line Control in End-Fired Furnaces
The foam line reflects glass melting and refining quality during production. While ordinary glass products in end-fired furnaces have no strict foam line requirements, high-quality glass products demand precise control. Due to the long flame path in end-fired furnaces - following a U-shaped route along the furnace‘s longitudinal axis - the hotspot cross-section presents an arc shape.
The ideal melting condition shows mirror-like surfaces without scum or bubbles in areas near the throat and two right-angle zones. The boundary between this mirror surface and floating scum constitutes the foam line. Larger mirror areas indicate better foam lines and superior glass refining quality. The foamy scum area fluctuates with firing reversals and batch feeding rates.
Key technical measures for foam line control:
(1) Thin-layer uniform feeding: Thick batch layers from concentrated feeding may allow unmelted material to bypass the refining zone, causing inclusions in final products. Optimal thickness varies by glass type (90-150mm for container glass).
(2) Adjust flame intensity according to pull rate changes: Unadjusted heat input leads to significant hotspot and foam line variations.
(3) Modify flame parameters when formula or batch quality changes: Formula adjustments affect melting capacity and layer thickness. Monitor foam line position closely and adjust temperature profiles accordingly.
3.4 Furnace Pressure Control
As a critical parameter, slight positive pressure (2-4Pa at glass level, 12-20Pa at crown) must be maintained throughout the furnace. Excessive pressure destabilizes melting, impedes refining, increases energy consumption, and accelerates refractory erosion. Insufficient pressure (especially negative pressure at glass level) disrupts flame patterns, reduces melting efficiency, and hinders bubble removal.
Operators should observe:
Gentle exhaust flow at charging end
Appropriate flame length at breastwall observation holes
Key influencing factors include:
Ambient temperature/pressure
Regenerator resistance
Flue temperature/damper position
Fuel/combustion air flows
Automatic pressure control systems should maintain stability through coordinated adjustment of these parameters. Common pressure spikes often result from:
Water accumulation in flues
Ash deposition
Regenerator blockages
3.5 Glass Level Control
Stable glass level (±0.5mm, or ±0.1mm for precision production) is crucial for melting/forming quality and furnace longevity.
Primary influencing factors are:
Batch feeding rate (direct impact)
Furnace pressure fluctuations (especially during reversals)
Modern level control instruments (laser, nuclear, or image-based) significantly reduce fluctuations. End-fired furnaces predominantly use laser level sensors for their high precision, low cost, and easy maintenance.
The molten glass is highly sensitive to changes in furnace flame atmosphere, which significantly affects:
►Refining and homogenization processes
►Product characteristics (color, transmittance, surface quality)
►Various physicochemical reactions (water evaporation, salt decomposition, oxidation of organics/carbon/sulfides, crystalline transformations)
Improper control may cause product defects. The atmosphere should be strictly controlled according to technical requirements:
►Oxidizing atmosphere: Suitable when batch contains minimal oxides/carbon, with low viscosity and high iron content►Reducing atmosphere: Preferred for opposite conditions
►Container glass production: Weak reducing atmosphere at the hotspot promotes rapid homogenization and bubble removal
Atmosphere is determined by oxygen/reducing components percentage in combustion products. Stable combustion atmosphere must be maintained alongside the four fundamental stabilities (raw materials, fuel, melting, forming).
The green, environmentally friendly, healthy, innovative, and high-quality development of daily-use glass enterprises will be the main theme of social progress. Deepening the integration of advanced manufacturing and modern service industries aligns with the new wave of technological revolution and industrial transformation.
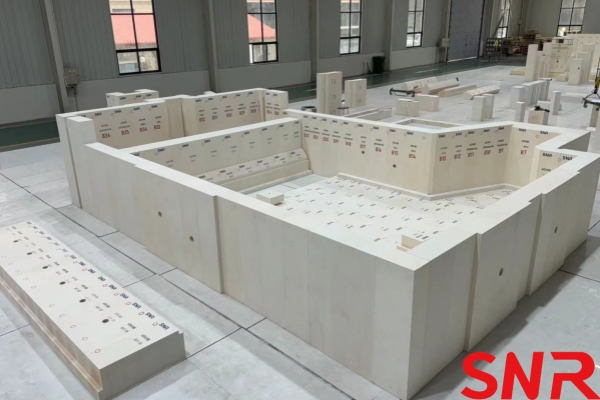
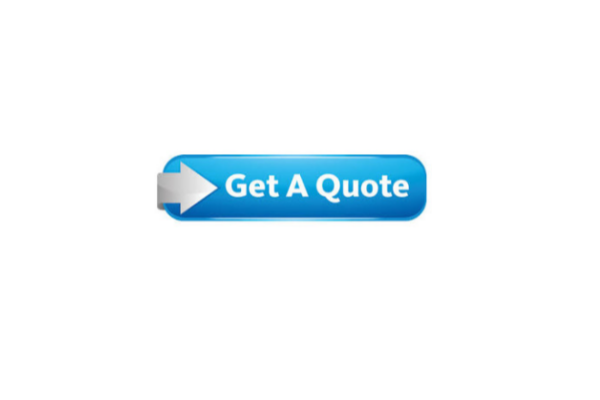
Henan SNR Refractory Co., Ltd. has been specializing in the production of fused cast AZS blocks for about 25 years. We use high-quality raw materials and advanced fusion technology to provide customers with high-quality products. From raw material procurement to finished product delivery, every step is strictly quality inspected to ensure that every indicator meets the standards, so you can use it with confidence.
If you have any needs, you can contact me at any time.
Web:www.snr-azs.com
Email: wendy@snrefractory.com