At present, the sidewall blocks of the melting zone of ordinary glass furnaces generally adopt an overall sidewall shallow tank structure with a thickness of 250 mm and a height of about 1,350 mm. The sidewall blocks are made of fully oxidized void free cast fused cast AZS blocks. Generally, fused cast AZS # 36 blocks is used in the melting zone, fused cast AZS # 33 blocks is used in the clarification zone, and fused cast AZS # 41 blocks is used in the corners. Under the same quality conditions, high-grade blocks have stronger corrosion resistance, but when the erosion residue is less than 50 mm, high-grade blocks are prone to bursting. There are also designs with layered structures or deep tank structures. With the increase of furnace age and the use of lower-layer insulation and bubbling, the erosion of the lower sidewall is large and difficult to check. Some manufacturers have very thin lower sidewalls when releasing water, so the quality of the lower sidewalls should also be taken seriously. In order to gradually extend the service life of glass furnaces, the production technology of fused cast AZS blocks has been improved, and it is also crucial to use sidewall blocks well.
►Characteristics of fused cast AZS blocks
►Heating up of sidewall blocks
►Erosion mechanism of sidewall blocks
►AZS patching blocks of sidewall
I Characteristics of fused cast AZS blocks
There are many companies producing fused cast AZS blocks (fused zirconium corundum blocks) for glass furnaces at home and abroad, and the product quality level and price vary greatly. Many manufacturers at home and abroad have a lot of room for improvement in appearance quality, composition design, casting process and dimensional accuracy. The quality of blocks directly affects the service life of the sidewall, especially the crystal structure, glass phase content and processing accuracy of blocks.
Due to its dense structure and low porosity, the fused refractory material has an extremely high Young’s modulus below 800 ℃, is very brittle, has a large cold compressive strength of more than 350 MPa, but has a tensile strength of only about 20 MPa. When subjected to thermal shock and uneven heating, the tensile stress caused by the temperature difference is too large and the volume changes too fast, and there is no pore to buffer, so it is very easy to burst.
The figure below shows the physical and chemical properties of fused cast AZS #33 blocks:
II.Heating up of sidewall blocks
During the heating process of the fused cast AZS sidewall block in the glass furnace,
When the temperature is between 0 and 1 100 ℃, the block gradually expands linearly with the increase of temperature, and the linear expansion of this process is about 0.8%.
When the temperature is between 1 100 and 1 200 ℃, the monoclinic ZrO2 in the block body transforms into tetragonal ZrO2, accompanied by the change of volume, the block body shrinks, and the total expansion rate drops from about 0.8% to about 0.6%;
when the temperature is higher than 1 200 ℃, the block starts to expand again with the increase of temperature;
Below 1 600 ℃, the overall expansion of the sidewall block is not large, and the average expansion coefficient is about 7×10-6/℃
During the glass furnace heating process, the maximum tensile stress appears in the non-insulated area on the upper part of the sidewall block, close to the cold face of the block, and increases with the increase of temperature until the temperature stabilizes. When the cooling air starts to blow, the tensile stress of the block body has a short peak value. Therefore, when the stress is relatively small, that is, when the furnace temperature is lower than 700 ℃, the air is added step by step, and the number of cracks generated is relatively small. Because of the insulation of the lower layer, the stress in the longitudinal direction of the sidewall is greater than the stress in the vertical and thickness directions of the sidewall, which often exceeds the tensile strength limit of the block material.
Therefore, longitudinal cracks generally appear in the sidewall blocks during the glass furnace heating process. Generally, they appear in two periods: a period of time after the cooling air is turned on and when the glass furnace temperature is 950~1200 ℃. The cracks develop in the thickness and vertical direction of the block. When the glass furnace temperature is 900~1200 ℃, the heating rate should not be too fast, and it is generally required not to exceed 15 ℃/h. When the internal temperature of the block body is greater than 1000 ℃, the block body is plastic and can completely absorb the stress and cracks generated, and the cracks are also bridged. The cracks generated by the glass furnace will not spread to the hot face and insulation area of the block.
Due to design and block laying reasons, expansion joints are reserved between sidewall blocks or joints in some places are not close together. During the glass furnace heating process, heat is dissipated at the straight joints, the temperature of the block edges rises, and the tensile stress moves from the outer surface of the block to the inside, causing stress changes, which may cause horizontal cracks. Therefore, pre-arrangement and precision processing of sidewall blocks are also very important.
During the casting process of fused cast AZS blocks, baddeleyite crystals are first crystallized and dispersed, forming a sponge-like framework. When corundum crystals are precipitated, they wrap baddeleyite crystals to form baddeleyite-corundum eutectics, and the final space is filled with glass phase and crystallized.
The sponge-like framework baddeleyite is very stable, but as time goes by, it is washed away by glass liquid, flame smoke and falls by its own gravity, exposing the new block surface to continue working and repeated erosion; after production is stopped, sponge-like baddeleyite frameworks on the surface of fused cast AZS blocks are often found in the flame space.
The liquid surface is subject to greater chemical erosion and mechanical scouring by the glass liquid. The glass gradually penetrates into the sponge-like frame of the block body and reacts with it and flows away. In addition, small bubbles in the glass phase continue to rise and stir the glass liquid, intensifying the reaction and scouring, making it corrode faster. The AZS material‘s resistance to glass liquid erosion is affected by the crystal size, number, arrangement and distribution of the glass phase, among which the number of eutectics and the proportion of baddeleyite crystals in the eutectics have the greatest influence.
IV.AZS patching blocks of sidewall
There are many factors that affect the service life of sidewall blocks, which are related to
►glass furnace heating,
►cooling of sidewalls,
►glass pulling amount,
►glass composition,
►production stability,
►direction of material piles, etc.
The service life of the weakest part of a 250 mm thick sidewall in normal use is 3 to 6 years. During use, the sidewall generally begins to turn red at the liquid surface line. As the redness becomes serious and accompanied by cracks, it eventually collapses. In the absence of cracks, blocks are usually patched when there are 20 to 30 mm left on the sidewall.
With the improvement of the quality of refractory materials and the level of glass production operation, the service life of float furnaces has been greatly extended. The age of many glass furnaces have exceeded 10 years, but patching blocks and replacing of sidewall blocks have become a necessary maintenance for every glass furnace.
AZS patching blocks is a project with high labor intensity, harsh working environment and high risk factor. Before patching AZS blocks, it is necessary to comprehensively consider various possible problems and make good preparations for work and emergency.
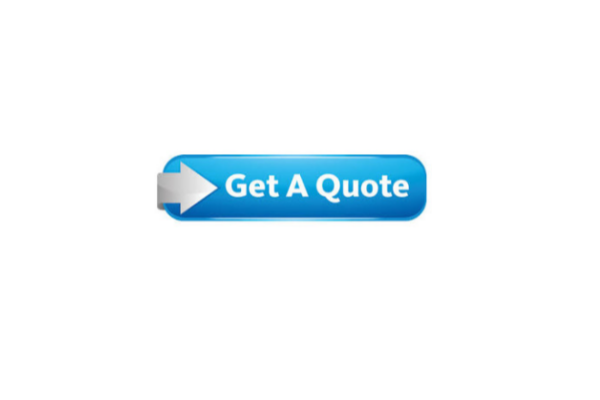
Figure shows the effect of twice patching 75 mm thick AZS blocks of sidewall.
The thickness of general AZS patching blocks is in the range of 75~150 mm. The service life of 75 mm thick AZS patching blocks is 1.5~3 years.
Due to the effect of cooling wind, the inner old sidewall usually collapses half a year after patching AZS blocks (the remaining amount of the original sidewall is about 30 mm); while the sidewall patched the 150 mm thick AZS blocks collapses very quickly, and the service life is only half a year to one year longer than the sidewall patched 75 mm AZS blocks. However, the labor intensity of patching 150 mm sidewall blocks is significantly increased.
►After the first patching of blocks, it is very easy to burn the breast wall support plate.
►During the second patching of blocks, the breast wall support plate is exposed to the flame space and is not conducive to maintenance and the patching of 75 mm thick sidewall blocks may cause the support plate to burn.
The glass furnace sidewall is often the weak link in the process of use. The service life of the glass furnace sidewall is affected by a variety of factors. From the initial design to the selection of refractory materials, furnace heating, the use of cooling air, glass production, daily maintenance, block patching, etc., they are all closely related. The design, production, use and maintenance of glass furnace sidewall blocks are being improved to ensure the safety of the glass furnace sidewalls throughout the life of the furnace. The service life of the glass furnace sidewall will be further extended in the future.
Henan SNR Refractory Co., Ltd.has been specializing in the production of fused cast AZS blocks for about 25 years. We use high-quality raw materials and advanced fusion technology to provide customers with high-quality products. From raw material procurement to finished product delivery, every step is strictly quality inspected to ensure that every indicator meets the standards, so you can use it with confidence.
If you have any needs, you can contact me at any time.
Web:www.snr-azs.com
Email:wendy@snrefractory.com