Glass furnaces are usually made of fused cast AZS blocks and are used as thermal equipment for melting glass.
According to the products manufactured, glass furnaces are categorized into flat and daily-use glass furnaces.The glass furnace is used to manufacture flat, embossed, filament, and other architectural glass plates.
According to the forming method, it is divided into float glass furnaces, lead glass furnaces, flat glass furnaces, and calendared glass furnaces.
This article studies the float glass furnace. As the main thermal equipment in the glass production process, its service life mainly depends on the erosion and burning degree of the glass furnace sidewall. The sidewall near the glass liquid level is the most severely eroded part of the glass furnace. Due to the sidewall near the glass liquid surface in the high-temperature environment by the flame radiation, glass liquid scouring, and chemical reaction with the material, the erosion rate is faster than other parts of the sidewall. Improper operation or maintenance in the production process will accelerate the erosion of the sidewall, which will affect the service life of the glass furnace and may also cause major safety accidents. In addition to affecting life and the existence of safety hazards, sidewall erosion will cause small particles to fall into the glass liquid, in the glass molding process to form stones, knots, bubbles, and other defects, which will affect the quality of glass production. Figure 1 is the structure of the float glass furnace, you can see the sidewall in the glass furnace in the position.
The length of service life of glass furnaces can reflect the development of glass furnace technology. At present, the domestic large-scale float glass furnace reasonable use of high-quality refractory materials, the service life of the glass furnace can reach 8 to 10 years, but there is still a large gap with the service life of foreign production lines 14 to 16 years. Float glass furnace sidewall blocks use fused zirconium corundum blocks, namely fused cast AZS blocks. Fused cast AZS blocks have low porosity, and the erosion rate of AZS blocks is proportional to the porosity. Its density and low porosity microstructure ensure that it has good thermal properties. At the same time, it can also prevent chemical reactions. Widely used in various glass furnaces melting end of the sidewall and breast wall and other parts.
2. Principle of heat transfer process through the sidewall of the glass furnace
3. Evaluation of the main factors of heat dissipation in the sidewall
4. Refractory materials used for sidewall blocks
1.1 Erosion mechanism of sidewall blocks
The erosion of the sidewall block by the glass liquid is a complex process. The sidewall block is subject to high-temperature flame radiation and the initialization of the airflow, which will cause the sidewall block to form an anti-corrosion protective layer and lose. The sidewall block is an acidic refractory material, so the alkaline oxide in the compounding material is the main component that causes the sidewall erosion. The alkaline oxide adheres to the surface of the sidewall block and diffuses to the inside, reducing the melting temperature of the glass phase, making the glass phase in the sidewall block easier to seep out, so that the sidewall block is eroded and falls off. There is a horizontal and longitudinal temperature difference in the glass liquid level inside the glass furnace. The complex convection of the glass liquid, which constantly initializes the sidewall, will also cause the erosion-resistant protective layer to be lost, thereby accelerating the erosion rate of the sidewall block. Overall, under the action of heat, chemistry, and machinery, the sidewall blocks are gradually eroded.
1.2 Factors affecting the erosion of sidewall blocks
(1) Sidewall block composition and quality.
Some impurities in the sidewall blocks will form eutectic substances with silica, the viscosity of the glass phase will become smaller at high temperatures, and the exudation temperature of the glass phase will become lower, which will accelerate the erosion rate of the sidewall blocks. The existence of pores in the sidewall will also accelerate the erosion of the sidewall blocks.
(2) Glass composition.
The erosion rate of the mirabilite compound on the sidewall blocks is greater than that of the soda ash compound, and the erosion range of mirabilite is also larger than that of molten soda ash. Mirabilite compound can erode almost the entire sidewall blocks, while molten soda ash only erodes the fused cast AZS blocks near the doghouse.
(3) The working temperature of the glass furnace.
The increase in the melting end temperature of the glass furnace can not only intensify the erosion chemical reaction but also accelerate the diffusion and dissolution speed, which may cause abnormal erosion of the sidewall blocks. Every increase in the melting temperature of the glass furnace by 50-60 ° C will double the erosion speed and greatly shorten the life of the sidewall blocks.
(4) Glass furnace discharge.
The large amount of discharge means that the glass liquid circulates less times in the glass furnace and the retention time is short, the glass liquid flow rate is fast, the initialization of the sidewall is intense, and the erosion speed of the sidewall blocks is fast.
(5) Glass furnace heating curve.
During the heating process of the glass furnace before production, the temperature changes rapidly, and the sidewall blocks are prone to cracks.
(6) The glass level fluctuates.
The temperature difference between the two sides of the glass furnace is too large, which intensifies the fluctuation of the liquid level and accelerates the erosion rate of the sidewall blocks.
1.3 Sidewall block erosion control
The erosion of the sidewall block surface directly in contact with the glass liquid is inevitable, and the erosion speed of the sidewall block can only be slowed down by suitable methods and means. Generally, the following measures are taken to delay the erosion of the sidewall block:
(1) Composition adjustment.
The complexes in the glass raw materials have serious erosion on the sidewall blocks, so the proportion of alkali and mirabilite in the complexes can be appropriately reduced without affecting the physical properties of the glass.
(2) Melting process.
Optimize the melting process to ensure the stability of the glass furnace temperature, the position of the stack, and the glass liquid surface.
(3) Sidewall wind control.
Determine the horizontal distance of the trend from the sidewall block and the vertical distance from the glass liquid surface, and maximize its effectiveness under the same wind speed.
Try to ensure that the air volume and strength of the cooling air are stable, and adjust the air volume in time according to the degree of erosion of the sidewall blocks.
Reduce the cooling air temperature of the sidewall, improve the cooling effect, and slow down the erosion rate of the sidewall blocks.
2. Principle of the heat transfer process of glass furnace sidewall
2.1 Heat transfer
The heat transfer process is a complex thermal energy transfer process, which refers to the process of heat transfer from the fluid on one side of the sidewall to the fluid on the other side through the sidewall. According to its physical nature, heat transfer phenomena can be divided into three basic ways: heat conduction, convection, and radiation. The three basic ways of heat transfer in a glass furnace exist simultaneously, and this process is called a comprehensive heat transfer process. Heat transfer in a glass furnace is very complicated.
The flame transfers heat to the glass surface through convection and radiation. After the glass surface absorbs part of the radiant energy, the rest is reflected. When passing through the gas layer, part of it is absorbed by the gas layer, and the remaining part falls on the inner wall of the sidewall;
At the same time, the flame transfers heat to the inner wall of the sidewall in the same way, absorbs some of the radiant energy, and reflects the rest. When passing through the gas layer, part of it is absorbed by the gas layer, and the passing part falls on the glass liquid surface. After the glass liquid partially absorbs the radiant energy, the rest is reflected;
Similarly, the radiant energy emitted by the inner wall of the sidewall is partially absorbed when it passes through the gas layer, and some of it falls on the glass liquid surface and the inner wall of the sidewall respectively. After the radiant energy is partially absorbed, the remaining part is reflected by the liquid surface and the inner wall of the sidewall respectively.
The above is how the heat is obtained by the sidewall and the glass liquid surface that have not been in contact with the glass liquid. The glass liquid is transferred to the inner wall of the sidewall in contact with the glass liquid by convection heat transfer; then the inner wall of the sidewall is transferred to the outer wall of the sidewall by solid heat conduction; finally, the outer wall of the sidewall is lost to the surrounding environment through the radiation between the outer wall surface and the environment and the convection heat transfer with the air. Heat transfer from the high-temperature inner
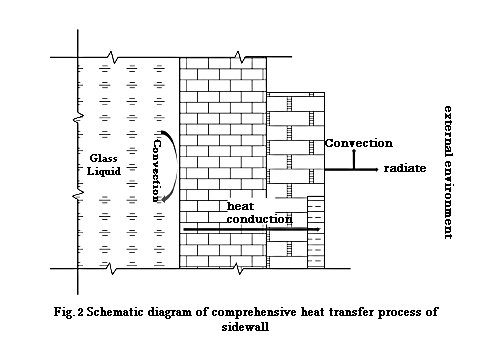
wall surface of the sidewall block to the low-temperature outer wall surface, that is, heat conduction through the sidewall, its heat flow is equal to the sum of the heat lost from the outer wall surface through convection and radiationFig.2 shows the comprehensive heat transfer process of the sidewall.
The convection heat transfer on the inner wall of the sidewall is mainly forced convection, and the high-temperature glass liquid in the glass furnace belongs to the forced convection heat transfer on the cold wall. The solid wall conducts heat, and most of the sidewalls that contact the glass liquid are multi-layer sidewalls. It is assumed that there is no contact thermal resistance between layers. When there is no ventilation on the outer wall of the sidewall, convection belongs to natural convection heat transfer; when there is forced wind, convection belongs to forced convection heat transfer.
2.2 Solid thermal conductivity of sidewall
When there is no relative displacement between various parts of an object, the heat transfer generated by the thermal motion of microscopic particles such as molecules, atoms, and free electrons is called heat conduction, or heat conduction for short. The laws of heat conduction phenomena have been summarized as Fourier‘s law.
The value of thermal conductivity depends on factors such as the type of material and temperature. Thermally conductive materials in engineering applications are divided into four types according to their thermal conductivity:
♦uniform and isotropic,
♦uniform and anisotropic,
♦inhomogeneous and isotropic,
♦inhomogeneous and anisotropic.
Sidewall blocks belong to uniform and isotropic materials, which is conducive to the calculation of the thickness of sidewall blocks.
To determine the heat flux value, it is necessary to determine the temperature field inside the sidewall, which requires combining three-dimensional thermal conductivity differential equations, namely:
The above three-dimensional thermal conductivity differential equation is a general form in the Cartesian coordinate system, and its corresponding simplified form can be obtained for specific situations.
2.3 Convective heat transfer between the inner and outer walls of the sidewall
Convective heat transfer refers to the process of heat transfer between the fluid and the surface of an object when an object flows over the surface of an object. The basic calculation formula for convective heat transfer is the Newton cooling formula, which is as follows:
In the process of convective heat transfer, the size of the surface heat transfer coefficient is affected by many factors. Mainly include the following aspects:
First, the cause of fluid flow. Natural convection and forced convection have different causes, which will lead to differences in heat transfer laws and heat transfer coefficients.
Secondly, whether the fluid undergoes a phase change. The heat transfer mode in the phase change state is different from that in the absence of phase change.
Similarly, changes in the flow state will also affect the heat transfer coefficient. The heat transfer coefficient of turbulent flow is greater than that of laminar flow.
In addition, the geometric factors of the heat transfer surface, including shape, size, roughness, and the direction of relative fluid motion, also affect the heat transfer law, resulting in differences in heat transfer coefficients.
Finally, the physical properties of the fluid, such as density, dynamic viscosity, and thermal conductivity, affect heat exchange, which in turn causes changes in the heat transfer coefficient.
2.4 Radiant heat transfer on the outer wall of the sidewall
Objects in nature emit thermal radiation into space all the time, while constantly absorbing thermal radiation from other objects. The combined result of outward radiation and absorption processes results in the transfer of heat between objects in the form of radiation, which is called radiative heat transfer. The fourth power law for calculating the radiant force on the outer wall of a sidewall block is as follows:
The emissivity of the surface of an object depends on the type of substance, surface temperature, and surface conditions. The emissivity of different types of substances varies, and the emissivity of the same object varies with temperature. Surface conditions have a great influence on emissivity. Metal materials with highly polished surfaces often have lower emissivity than rough surfaces and surfaces subject to oxidation. Most non-metallic materials have high emissivity values, with the emissivity of sidewall blocks being 0.8.
3. Evaluation of the main factors of sidewall heat dissipation
3.1 The influence of the trend horizontal distance on the heat dissipation effect
Taking the erosion of the 50 mm sidewall block as an example, the influence law on the heat dissipation effect of the sidewall is studied by changing the horizontal distance between the trend and the sidewall block. In terms of specific factor settings, the distances are set to 30, 35, 40, 45, 50, 55, and 60mm respectively. To control the variables to ensure the comparability of the simulation results, other boundary conditions such as wind speed remain consistent.
Figure 7-1 shows the changes in physical quantities on the outer wall of the sidewall tiles at different horizontal distances.
It can be seen from Figure (a) that with the increase of the horizontal distance from the sidewall block, the average convective heat flux density of the outer wall surface decreases, indicating that the heat transfer of the outer wall surface through convective heat transfer decreases, resulting in an increase in the temperature of the outer wall surface.
As can be seen from Figure (b), the horizontal distance from the trending sidewall is from 30mm to 60mm, and the average temperature difference of the outer wall surface reaches 25 K.
►The horizontal distance increased by 16.7%, the average convective heat flux of the outer wall decreased by 0.33%, and the average temperature of the outer wall increased by 0.68%.
►The horizontal distance increased by 33.3%, the average convective heat flux on the outer wall decreased by 0.77%, and the average temperature on the outer wall increased by 1.07%;
►The horizontal distance increased by 50%, the average convective heat flux on the outer wall decreased by 1.45%, and the average temperature on the outer wall increased by 1.69%:
►The horizontal distance increased by 66.7%, the average convective heat flux of the outer wall decreased by 1.98%, and the average temperature of the outer wall increased by 1.91%.
►The horizontal distance increased by 83.3%, the average convective heat flux on the outer wall decreased by 2.46%, and the average temperature on the outer wall increased by 2.28%;
►The horizontal distance increased by 100%, the average convective heat flux on the outer wall decreased by 2.91%, and the average temperature on the outer wall increased by 2.64%.
Figure 7-2 shows the average temperature of the inner wall of the sidewall block at different horizontal distances. It can be seen from the figure that with the gradual increase of the horizontal distance, the average temperature of the inner wall surface shows an overall increase trend. This is because the thermal boundary conditions remain unchanged, the convective heat transfer on the outer wall of the sidewall block decreases, which in turn leads to the increase of the inner wall surface temperature. The horizontal distance from the sidewall block is from 30mm to 60mm, and the average temperature difference of the inner wall surface is 3K. The horizontal distance is from 30mm to 40mm, and the average temperature of the inner wall surface increases significantly; the horizontal distance is from 40mm to 60mm, and the average temperature of the inner wall surface increases more gently.
Figure 7-3 shows the velocity cloud diagram of the outer wall surface of the sidewall block at different horizontal distances. Figures (a), (b), (c), and (d) show the velocity cloud diagram of the outer wall surface at a horizontal distance of 30, 40, 50, and 60 mm, respectively. As the horizontal distance increases, the cross-sectional velocity at the same position gradually decreases. Two areas below the cloud image are different from other edge areas, and their velocities are higher because there is a 25 mm gap between the thermal insulation blocks, and there is an airflow passing through them. Analyzing the cloud image data, it is known that:
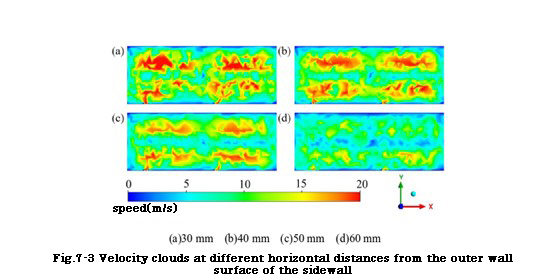
►When the horizontal distance is 30mm, the area with a speed greater than 15 m/s accounts for 21.3%;
►When the horizontal distance is 40mm, the area with a speed greater than 15 m/s accounts for 18.9%;
►When the horizontal distance is 50mm, the area with a speed greater than 15 m/s accounts for 14.4%.
►When the horizontal distance is 60 mm, the area with a speed greater than 15 m/s accounts for 0.67%.
3.2 The influence of the vertical distance of the trend on the heat dissipation effect
The previous section studied the influence of the horizontal distance on the heat dissipation effect of the sidewall, and this section studied the influence of this factor on the heat dissipation effect of the sidewall by changing the vertical distance of the trend from the glass liquid surface. In terms of specific factor settings, under the premise of the horizontal distance of 50 mm and the wind speed of 20 m/s, the vertical distance is set to 30, 40, 50, 60, 70, 80, and 90 mm respectively.
Figure 7-4 shows the average convective heat flux density of the outer wall surface at different vertical distances. It can be seen from the figure that with the increase of the vertical distance between the outgoing trend and the glass liquid surface, the average convective heat flux density of the outer wall surface increases first and then decreases. When the vertical distance between the outgoing trend and the glass liquid surface is 60mm, it reaches the maximum value. This is because the vertical distance outgoing trend at this time is about in the middle position of the outer wall surface of the non-insulated part of the sidewall block, and the distance traveled by the airflow up or down after blowing to the sidewall is the same. The difference in the average heat flux density of the vertical distance of the different outgoing trends is less than the difference in the average heat flux density of the different horizontal distances, and the vertical distance is less than the effect.
Figure 7-5 shows the average temperature of the inner wall of the sidewall block at different vertical distances. It can be seen from the figure that with the gradual increase of the vertical distance, the average temperature of the inner wall surface shows a small-range downward trend. The value range of the average temperature of the inner wall surface is part of the contact with the glass liquid. With the downward movement of the trend position, the radiation of the high-speed airflow to the inner wall value range becomes larger, so the average temperature of the inner wall surface decreases in a small range. The vertical distance of the trend from the sidewall block is from 30mm to 90mm, and the average temperature difference of the inner wall surface reaches 6K. The vertical distance is from 70mm to 90mm, and the average temperature of the inner wall surface is stable.
Figure 7-6 shows the velocity cloud diagram of the outer wall surface of the sidewall block at different vertical distances. Figures (a), (b), (c), and (d) show the velocity cloud diagram of the outer wall surface at vertical distances of 30, 50, 70, and 90 mm, respectively. As the trend position moves down, the high-speed area moves down correspondingly, corresponding to a small range of decreases in the average temperature of the inner wall surface. Analyzing the cloud image data, it is obtained that:
►When the vertical distance is 30 mm, the area with a speed greater than 10 m/s accounts for 8.1%.
►When the vertical distance is 50 mm, the area with a speed greater than 10 m/s accounts for 9.3%.
►When the vertical distance is 70 mm, the area with a speed greater than 10 m/s accounts for 10.7%.
►When the vertical distance is 90mm, the area with a speed greater than 10m/s accounts for 10.7%.
According to the above area ratio greater than 10m/s, the vertical distance has little effect on the radiation range of the same speed.
3.3 Summary
As far as the average heat flux of the outer wall surface of the sidewall block is concerned, the order of the influence degree of each factor is: the horizontal distance between the trend and the sidewall block, the size of the wind speed, and the vertical distance between the trend and the glass liquid surface;And the impact of these three factors on it is very significant.
As far as the average temperature of the inner wall surface of the sidewall block is concerned, the order of the influence degree of each factor is: the horizontal distance from the sidewall block, the size of the wind speed, and the vertical distance from the glass liquid surface; But the effect of the three factors was not significant.
When the horizontal distance from the sidewall block increases to 50 mm, the proportion of the speed greater than 15 m/s decreases sharply; the horizontal distance increases from 30mm to 60mm, the temperature difference of the outer wall surface can reach 25K, and the temperature difference of the inner wall surface is 3K. With the increase of the vertical distance from the glass surface, the heat dissipation effect of the sidewall increases first and then decreases, and the proportion of the speed greater than 10m/s does not change much; when the vertical distance is 60mm, the heat dissipation effect of the sidewall is the best.
The results of the orthogonal test on the factors affecting the heat dissipation of the sidewall show that the horizontal distance between the trend and the sidewall block has the greatest influence on the average heat flux of the outer wall surface of the sidewall block, and the vertical distance between the trend and the glass liquid surface has the smallest influence on it; the variance analysis shows that the influence degree is all highly significant. The horizontal distance between the trend and the sidewall block has the greatest influence on the average temperature of the inner wall surface of the sidewall block, and the vertical distance between the trend and the glass liquid surface has the smallest influence on it; the variance analysis shows that the influence degree is all insignificant.
4. Refractory materials used for sidewall blocks
1. High alumina block
The main component of high-alumina blocks is alumina (Al2O O), with content generally between 48% and 90%. The higher the alumina content, the better its fire resistance. Its fire resistance is usually between 1770 and 1850 ° C.
Application scenarios: Widely used in the walls of various high-temperature industrial furnaces, such as glass furnaces, ceramic furnaces, etc. In glass furnaces, high-alumina blocks can resist the erosion of glass liquid because of their good chemical stability. Under high temperature and glass liquid initialization, they can maintain a long service life.
2. Clay blocks
Clay blocks are mainly made of refractory clay and contain a certain amount of SiO2 (about 50% - 60%) and Al2 O3 (about 30% - 40%). The advantage is that the price is relatively low, and the fire resistance is generally between 1580 and 1770 ° C. It has good thermal stability and can withstand a certain degree of temperature change without cracking.
Application scenarios: It is often used for some sidewalls that do not require particularly high temperatures, such as small heating furnaces, drying furnaces, etc. In some cost-sensitive and relatively mild temperature environments, clay blocks are an economical choice.
3. Magnesia brick
The main component of magnesia brick is magnesium oxide (MgO), the content is usually more than 80% - 90%. It has good resistance to alkaline erosion because magnesium oxide is chemically stable in alkaline environments. At the same time, magnesia bricks have high refractoriness, generally around 2000 ° C, and can withstand high-temperature environments. Its thermal conductivity is good, which helps to transfer heat and distribute it evenly.
Application scenario: suitable for sidewalls in alkaline environments
4. Fused cast AZS block
The main component of fused cast AZS block is alpha-alumina (alpha-AlO), and its alumina content is as high as 90% - 99%. Fused cast AZS block has extremely high hardness, good wear resistance, and excellent chemical stability, and can resist the erosion of a variety of acid and alkali media. Its refractoriness can reach more than 1800-2000 ° C, and it hardly reacts with other substances at high temperatures.
Application scenarios: Some sidewalls require extremely high corrosion resistance and high-temperature resistance. For example, in high-temperature furnaces that produce special ceramics, fused cast AZS blocks can ensure the stability of the side wall under high temperatures and complex chemical environments and ensure product quality.
Henan SNR Refractory Co., Ltd. is dedicated to the manufacturing and research and development of fused cast AZS refractory materials for the glass industry. Meanwhile, SNR can provide total solutions and services for glass furnace design, glass furnace construction, renovation and upgrading. Please contact me if you have any requirement.